I.Introduction
Liquid cold plates, manufactured by KenFa Tech, stand as indispensable components within thermal management systems, essential for efficiently dissipating heat produced by high-power electronic devices. Whether it’s CPUs in data centers or power electronics in electric vehicles, the reliability and performance of these devices hinge on effective cooling mechanisms.
Microchannel geometry emerges as a critical facet in optimizing liquid cold plate functionality. These intricate passages, meticulously designed to facilitate coolant flow, are pivotal in enhancing heat transfer efficiency. Within this framework, KenFa Tech has been at the forefront, integrating innovative microchannel designs to advance the thermal performance of their liquid cold plates.
This article embarks on a journey to explore the fundamental principles underlying liquid cold plates and underscores the pivotal role of microchannel geometry in augmenting heat dissipation. Furthermore, it sheds light on KenFa Tech’s commitment to innovation in microchannel design, aiming to deliver cutting-edge solutions to users across diverse industries.

II.Fundamentals of Microchannel Geometry
Definition and Role of Microchannels within Liquid Cold Plates
Microchannels represent intricate passages within liquid cold plates through which coolant circulates to absorb and dissipate heat. These channels are meticulously designed to facilitate efficient heat transfer from electronic components to the cooling fluid. Microchannels optimize thermal conductivity by maximizing surface area and promoting turbulent flow, ensuring effective heat dissipation.
Overview of Key Parameters Affecting Heat Transfer within Microchannels
Several vital parameters significantly influence heat transfer within microchannels, ultimately impacting the overall thermal performance of liquid cold plates:
- Aspect Ratio: The aspect ratio, defined as channel height to channel width, is crucial in determining flow behavior and heat transfer characteristics. Higher aspect ratios tend to promote turbulent flow, enhancing heat transfer efficiency.
- Hydraulic Diameter: Hydraulic diameter, a measure of the effective cross-sectional area available for fluid flow, directly affects flow resistance and heat transfer. Smaller hydraulic diameters result in increased flow velocities and convective heat transfer rates.
- Cross-Sectional Shape: The geometric configuration of microchannels, including rectangular, circular, or triangular cross-sections, influences fluid flow patterns and heat transfer mechanisms. Different shapes offer varying degrees of turbulence and surface area, impacting overall thermal performance.
Understanding and optimizing these critical parameters are essential for designing microchannels that maximize heat transfer efficiency within liquid cold plates. Manufacturers can tailor microchannel geometries to meet specific cooling requirements and enhance overall thermal management capabilities by carefully controlling aspect ratios, hydraulic diameters, and cross-sectional shapes.
III.Advancements in Microchannel Geometry
Enhanced Surface Area Designs
Introduction to Microchannel Designs with Increased Surface Area-to-Volume Ratios
Microchannel designs incorporating increased surface area-to-volume ratios have garnered significant attention in liquid cold plates. These innovative designs feature intricate geometries that maximize the contact area between the coolant and the surrounding surfaces. These microchannels facilitate more efficient thermal energy dissipation by amplifying the surface area for heat exchange.
Explanation of How Increased Surface Area Facilitates Better Heat Dissipation
The augmentation of surface area within microchannel designs translates to enhanced heat transfer capabilities. As coolant flows through the intricate network of channels, it comes into close contact with a larger surface area, promoting more effective heat dissipation. This intensified interaction between the coolant and the channel walls accelerates thermal energy transfer, improving cooling performance in liquid cold plates.
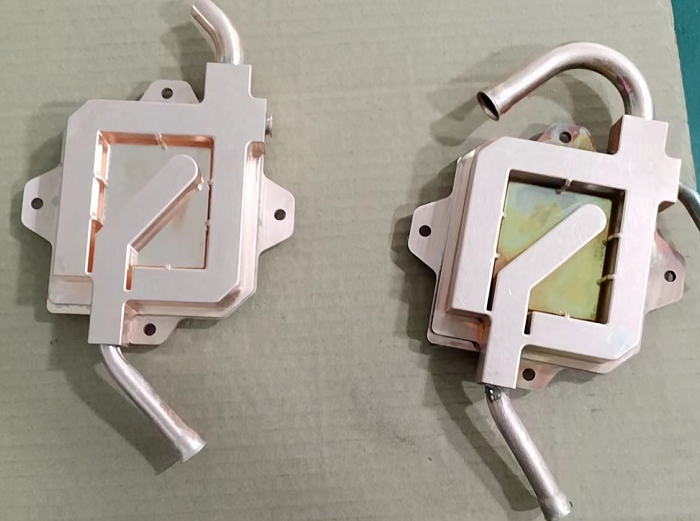
Optimized Channel Configurations
Exploration of Novel Channel Shapes and Arrangements (e.g., Serpentine, Zigzag)
Novel channel shapes and arrangements, such as serpentine and zigzag patterns, have become critical components of optimized microchannel geometry. These innovative configurations introduce deliberate disruptions in flow patterns, promoting turbulence and enhancing heat transfer efficiency. By strategically manipulating the coolant flow path, these optimized channel configurations facilitate more uniform heat distribution and minimize the formation of thermal gradients.
Discussion on How Optimized Configurations Minimize Thermal Resistance
Optimized channel configurations are designed to minimize thermal resistance within liquid cold plates, ensuring efficient heat transfer from electronic components to the cooling fluid. By reducing flow restrictions and enhancing convective heat transfer, these configurations mitigate heat buildup within the system. As a result, thermal energy is dissipated more effectively, maintaining optimal operating temperatures and prolonging the lifespan of electronic devices.
Integration of Nanoscale Features
Examination of Microchannels with Nanoscale Features (e.g., Fins, Roughness)
Microchannels with nanoscale features, such as Skived fins and surface roughness, represent a significant advancement in microchannel geometry. These nanofeatures introduce additional surface area and disrupt boundary layers, enhancing convective heat transfer. Nanoscale features facilitate more efficient heat dissipation within liquid cold plates by promoting fluid mixing and turbulence.
Explanation of How Nanofeatures Enhance Convective Heat Transfer
Integrating nanoscale features into microchannel designs augments convective heat transfer by optimizing fluid dynamics at the microscale. Fins and roughness elements disrupt laminar flow, promoting turbulent mixing and increasing heat transfer coefficients. This enhanced convective heat transfer ensures rapid removal of thermal energy from electronic components, contributing to the overall efficiency and reliability of liquid cold plate systems.
IV.Performance Benefits of Advanced Microchannel Geometry
Improved Thermal Conductivity
Case Studies Demonstrating Enhanced Heat Transfer Rates with Advanced Microchannel Designs
Several case studies have showcased the remarkable improvements in heat transfer rates achieved through advanced microchannel designs. By implementing intricate geometries that maximize surface area and promote turbulent flow, liquid cold plate manufacturers have observed substantial enhancements in thermal conductivity. These studies provide empirical evidence of advanced microchannel geometries’ superior heat dissipation capabilities, validating their efficacy in real-world applications.
Comparison of Performance Metrics with Traditional Liquid Cold Plate Configurations
A comparative Thermal Analysis between advanced microchannel designs and traditional liquid cold plate configurations underscores the former’s significant performance benefits. Through rigorous testing and experimentation, manufacturers have quantified the improvements in thermal conductivity achieved with advanced microchannel geometries. By contrast, traditional configurations exhibit higher thermal resistance and less efficient heat transfer, highlighting the superiority of advanced microchannel designs in optimizing thermal performance.
Enhanced Cooling Efficiency
Illustration of How Optimized Microchannel Geometry Reduces Thermal Gradients and Hotspots
Optimized microchannel geometry is pivotal in mitigating thermal gradients and hotspots within liquid cold plates. Advanced microchannel designs ensure a more uniform distribution of thermal energy by strategically manipulating flow patterns and enhancing convective heat transfer. This reduction in thermal gradients minimizes the risk of localized overheating, preserving the integrity of electronic components and extending their operational lifespan.
Discussion on the Impact of Improved Cooling Efficiency on System Reliability and Longevity
The enhanced cooling efficiency of advanced microchannel geometries translates to improved system reliability and longevity. By maintaining optimal operating temperatures and preventing thermal stress-induced failures, these designs contribute to the overall robustness of electronic systems. Moreover, mitigating thermal gradients and hotspots reduces the likelihood of performance degradation and extends the maintenance intervals of liquid cold plate systems. Consequently, users can expect enhanced reliability and prolonged operational lifespans from electronic devices integrated with advanced microchannel designs.
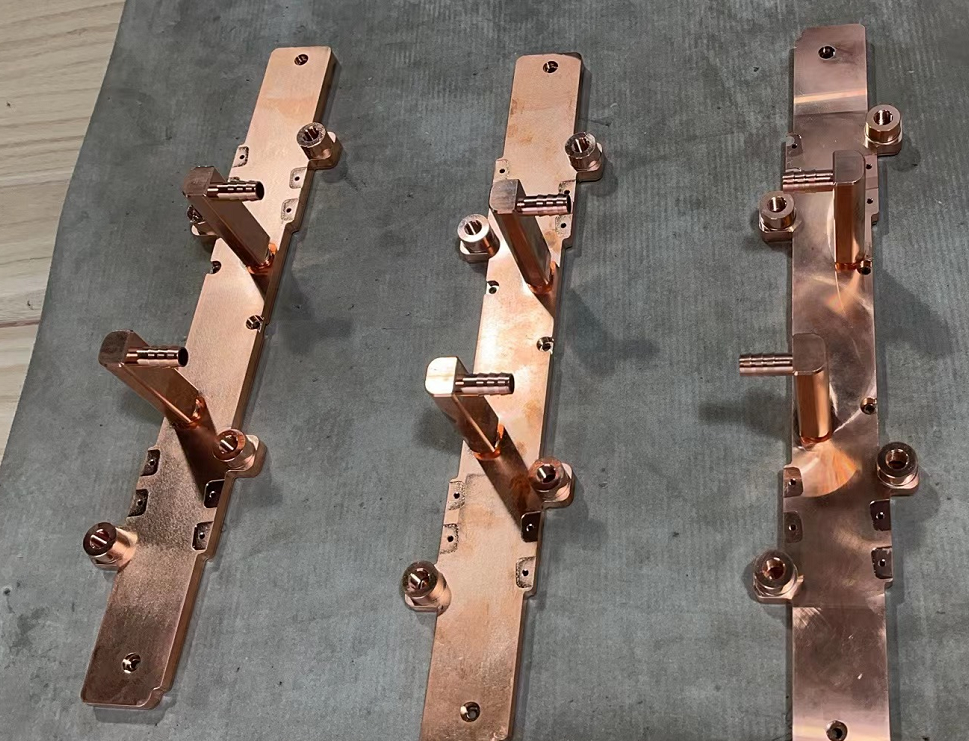
V.Practical Considerations for Users
Compatibility with Application Requirements
Guidance on Selecting Microchannel Designs Based on Specific Cooling Needs (e.g., Power Density, Flow Rate)
Users must assess their cooling requirements when considering liquid cold plates with advanced microchannel geometries. Power density, flow rate, and thermal load dictate the optimal microchannel design for a given application. Liquid cold plate manufacturers typically offer guidance and consultation services to assist users in selecting the most suitable microchannel configurations tailored to their cooling needs. By aligning the microchannel design with application requirements, users can optimize cooling efficiency and ensure optimal performance of electronic systems.
Manufacturing and Cost Implications
Evaluation of Manufacturing Feasibility and Cost Considerations Associated with Advanced Microchannel Geometries
Adopting advanced microchannel geometries may entail certain manufacturing complexities and cost considerations. Manufacturers must evaluate the feasibility of fabricating intricate microchannel designs and assess the associated production costs. Factors such as material selection, machining processes, and quality control measures impact advanced microchannel geometries’ manufacturing feasibility and cost-effectiveness. While these designs may incur higher upfront costs, the long-term benefits of improved cooling efficiency and system reliability often justify the investment for users.
Maintenance and Lifecycle Management
Recommendations for Maintenance Practices and Considerations for Prolonged Lifespan
Proper maintenance is essential to ensure liquid cold plates’ longevity and optimal performance with advanced microchannel geometries. Users should adhere to recommended maintenance practices, including regular cleaning, inspection, and preventive maintenance procedures. Additionally, considerations such as fluid compatibility, corrosion prevention, and system monitoring play crucial roles in prolonging the lifespan of liquid cold plate systems. Liquid cold plate suppliers may offer comprehensive maintenance and lifecycle management services to assist users in maximizing the performance and reliability of their cooling solutions throughout their operational lifespan.
Conclusion
The advancements in microchannel geometry represent a paradigm shift in liquid cold plate technology, offering unprecedented opportunities for enhancing heat transfer performance. Manufacturers have revolutionized the thermal management capabilities of liquid cold plates by leveraging intricate designs that maximize surface area, promote turbulent flow, and integrate nanoscale features. These advancements have led to significant improvements in thermal conductivity, cooling efficiency, and system reliability, addressing the evolving demands of industries reliant on high-performance electronics.
Looking ahead, the future of liquid cold plate technology holds immense promise, driven by ongoing innovations and advancements in microchannel geometry. Emerging technologies such as additive manufacturing, microfluidics, and nanotechnology are poised further to elevate the performance and versatility of liquid cold plates. Manufacturers continuously explore novel materials, manufacturing techniques, and design methodologies to push the boundaries of thermal management capabilities. As a result, we can anticipate continued enhancements in heat transfer efficiency, compactness, and customization options, ushering in a new era of liquid cold plate technology that meets the ever-growing demands of modern electronics.