Introduction
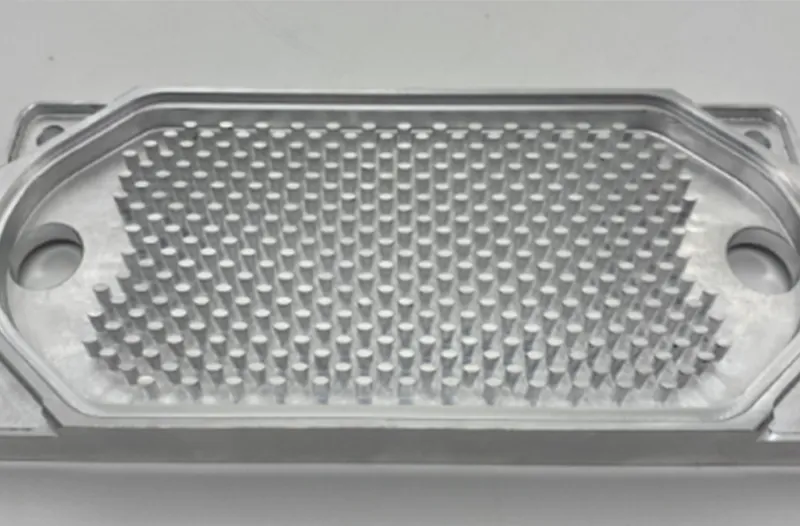
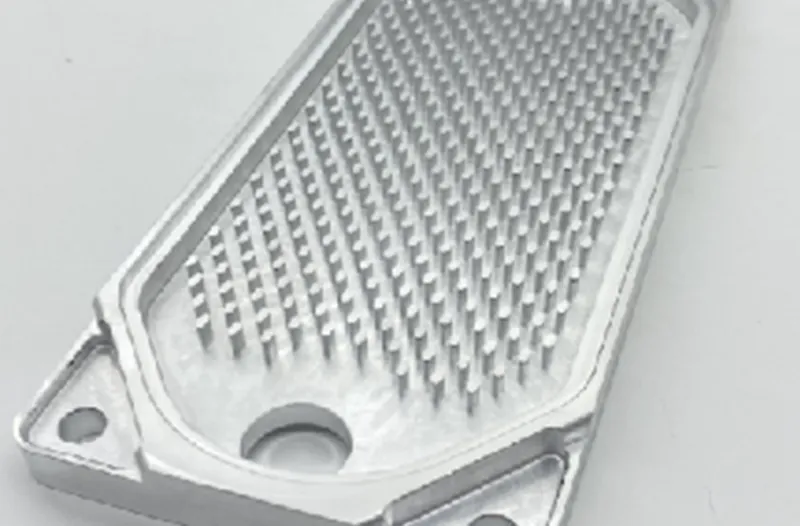
Heat sinks are crucial in aerospace and aviation industries, where efficient heat management is paramount. Excess heat can lead to severe consequences in these high-performance environments, including equipment failure and compromised safety. Cold forged heat sinks have emerged as a reliable solution to tackle this challenge, offering unique advantages that enhance heat dissipation capabilities. This article will explore the distinct features and benefits of cold forged and delve into their potential to revolutionize heat management in aerospace and aviation applications.
Understanding Cold Forging
Cold forging is a manufacturing process that involves shaping metal into desired forms without excessive heat. Unlike traditional techniques such as extruding or die casting, cold forging preserves the material’s structural integrity, resulting in superior mechanical properties. Cold forged heat sinks are fabricated with exceptional precision through controlled pressures and precise tooling, making them highly durable and reliable.
Basics of Heat Transfer in Aerospace
In the aerospace industry, effective heat dissipation is critical for maintaining optimum performance and reliability of aircraft and spacecraft systems. Excessive heat buildup can cause premature component failure, resulting in operational disruptions and safety hazards. Thus, managing heat transfer within these systems is of paramount importance. Heat sinks act as heat exchangers, absorbing and dissipating the unwanted thermal energy generated by electronic devices or other heat-emitting components.
The Unique Features of Cold Forged Heat Sinks
Enhanced Thermal Conductivity for Optimal Heat Dissipation
One key advantage of cold forged heat sinks is their exceptional thermal conductivity, which allows for efficient heat dissipation. Using materials like copper or aluminum, with high thermal conductivity, can swiftly transfer heat away from critical components, preventing overheating and ensuring optimal performance.
Lightweight and Compact Design
Cold Forged Radiator offer a remarkable advantage in their lightweight and compact design. Compared to traditional manufacturing techniques, cold forging allows for intricate designs and thin walls, reducing the overall weight and size of the heat sink. This benefit is invaluable in aerospace and aviation applications, where weight reduction significantly improves fuel efficiency and overall performance.
Resistance to Extreme Temperature and Vibration
Aerospace and aviation applications subject heat sinks to harsh environmental conditions, including extreme temperatures and vibrations. Cold forged heat sinks exhibit excellent resistance to such challenges, making them highly suitable for the demanding nature of these industries. Their robust construction ensures they can withstand extreme temperatures without compromising their structural integrity, providing long-lasting and reliable heat dissipation.
Improved Performance and Efficiency
Cooling Impact on Electronic Components
By effectively dissipating excess heat, cold forged heat sinks minimize the risk of thermal failure in electronic components. This directly translates to improved performance and longevity of critical systems, ensuring uninterrupted operation and increased overall efficiency. Additionally, well-designed heat sinks can maintain the temperature of sensitive electronic components within acceptable limits, further enhancing their reliability and performance.
Minimizing Thermal Resistance for Increased Reliability
Cold forged heat sinks are meticulously engineered to minimize thermal resistance, ensuring the efficient transfer of heat from hotspots to cooler regions. Heat sinks can effectively lower component temperatures with reduced thermal resistance, preventing overheating and potential damage to critical systems. The enhanced reliability resulting from this efficient heat dissipation promotes the longevity and stability of aerospace and aviation applications.
Reducing Power Consumption and Increasing Lifespan
Traditional cooling mechanisms often require high-energy consumption to maintain desirable temperature levels. However, Cold Forged Radiator offer a superior alternative by efficiently dissipating heat without excessive power requirements. This translates into reduced power consumption, optimizing energy usage and saving costs in the long run. Moreover, the extended lifespan of components achieved through effective heat management contributes to further cost savings and enhanced operational efficiency.
Tailoring Cold Forged Heat Sinks for Aerospace Applications
Cold forged heat sinks offer a wide range of customization options to cater to the diverse needs of aerospace applications. Manufacturers can tailor these heat sinks to meet specific requirements, considering size, shape, material, and cooling capacity. This flexibility enables the creation of heat sinks optimized for particular aircraft or spacecraft systems, ensuring efficient heat transfer and maximum performance.
Design Considerations for Efficient Heat Transfer
Various factors come into play when designing Cold Forged Radiator for aerospace applications to achieve optimum heat transfer. These considerations include the design of heat sink fins and base, geometry optimization, and air flow management. By fine-tuning these aspects, engineers can create heat sinks that effectively dissipate heat, maintain desired temperature levels, and overcome the challenges posed by restricted spaces and diverse equipment configurations within aerospace systems.
Integration with Existing Systems and Components
Cold forged heat sinks can seamlessly integrate with existing aerospace systems and components. This adaptability allows for easy retrofitting or upgrading of heat dissipation solutions without significantly modifying the overall system architecture. The compatibility of with existing setups ensures a smooth integration process, minimizing downtime and facilitating the overall efficiency and effectiveness of the aerospace application.
Cold Forged Heat Sinks vs. Traditional Cooling Solutions
Comparison with Extruded and Die-Cast Heat Sinks
Cold forged heat sinks offer distinct advantages over traditional cooling solutions, such as extruded and die-cast heat sinks. While extruded heat sinks are limited in terms of complex shapes and fins, cold forged provide greater design flexibility, creating intricate geometries that optimize heat dissipation. On the other hand, Die-cast heat sinks often suffer from porosity and reduced thermal conductivity, whereas cold forged exhibit superior structural integrity and enhanced thermal conductivity.
Advantages of Cold Forged Heat Sinks in Aerospace Applications
Cold Forged Radiator are advantageous in aerospace applications due to their lightweight design, enhanced thermal conductivity, and resistance to extreme conditions. These unique features ensure efficient heat dissipation while meeting stringent weight and performance requirements. Moreover, the customizability and compatibility of Cold forging technology further amplify their advantages in aerospace and aviation applications.
Aerospace Case Studies
Numerous success stories highlight the efficacy of cold forged heat sinks in aviation. Real-world examples demonstrate how these heat sinks have improved performance, increased reliability, and extended the lifespan of electronic components. Aerospace companies have reported significant improvements in thermal management and overall system efficiency by implementing Cold Forged Radiator, solidifying their position as a preferred choice in the industry.
Regulatory Compliance and Safety Measures
Regulatory compliance and safety are critical considerations in the aerospace and aviation industries. Cold forged heat sink manufacturers adhere to industry standards to ensure the reliability and safety of their products. Additionally, safety features, such as insulation and protective coatings, can be incorporated into heat sink designs to protect against potential hazards, ensuring safety and compliance within aerospace and aviation applications.
Future Prospects and Innovations
Advances in cold forging technology for heat sinks hold immense potential for the future of aerospace systems. Ongoing research and development efforts aim further to enhance the capabilities of cold forged heat sinks, enabling even more efficient heat transfer and improved performance. With the continual evolution of cold forging technology, the aerospace industry can look forward to next-generation heat management systems that optimize performance, reliability, and safety.
Cost-Effectiveness of Cold Forged Heat Sinks
Cold Forged Radiator offer significant economic benefits in aerospace and aviation applications. Their lightweight design leads to fuel savings and improved efficiency, contributing to long-term cost reductions. Moreover, the extended lifespan of electronic components achieved through efficient heat dissipation minimizes maintenance and operational costs, further enhancing the cost-effectiveness of Cold Forged Radiator in the aerospace industry.
Challenges and Limitations
Despite the numerous advantages, Cold Forged Radiator face challenges and limitations. Overcoming manufacturing complexities requires specialized expertise and equipment, potentially increasing production costs. Additionally, certain material limitations and design constraints associated with cold forged heat sinks must be carefully addressed to ensure optimal performance in specific aerospace and aviation applications.
Emerging Trends in Heat Sink Design
Integrating cold forged heat sinks with advanced cooling technologies presents an exciting trend in heat management. By combining cold forged with techniques like liquid cooling or phase-change materials, engineers can achieve even greater heat dissipation capabilities, pushing the boundaries of performance and reliability. Furthermore, the exploration of 3D-printed and nanomaterial heat sinks showcases the potential for groundbreaking advancements in the field, paving the way for highly efficient and compact heat dissipation solutions in aerospace and aviation.
Environmental Sustainability
Cold forging, as a manufacturing process, aligns with the principles of environmental sustainability. It involves minimal material wastage and energy consumption compared to traditional manufacturing techniques. Additionally, the materials used in cold forged heat sinks can be recycled, contributing to the overall sustainability of the aerospace and aviation industries. The eco-friendly nature of cold forging makes it an attractive choice for heat sink production, aligning with the growing focus on sustainability and green initiatives.
Conclusion
Cold Forged Radiator offer unique advantages, making them a perfect fit for aerospace and aviation applications. Their enhanced thermal conductivity, lightweight design, and resistance to extreme conditions contribute to improved critical systems’ performance, reliability, and lifespan. Customization options and seamless integration further enhance their applicability in diverse aerospace scenarios. As cold forging technology advances, the aerospace industry can anticipate a paradigm shift in heat management, resulting in increased efficiency, cost-effectiveness, and overall safety. Through their ability to revolutionize heat dissipation, cold forged heat sinks have the potential to transform the aerospace and aviation industries into more technologically advanced and reliable domains.