UPS (Uninterruptible Power Supply) is an electrical backup device designed to provide temporary power supply during main power source failures or fluctuations, ensuring continuous operation of critical equipment.
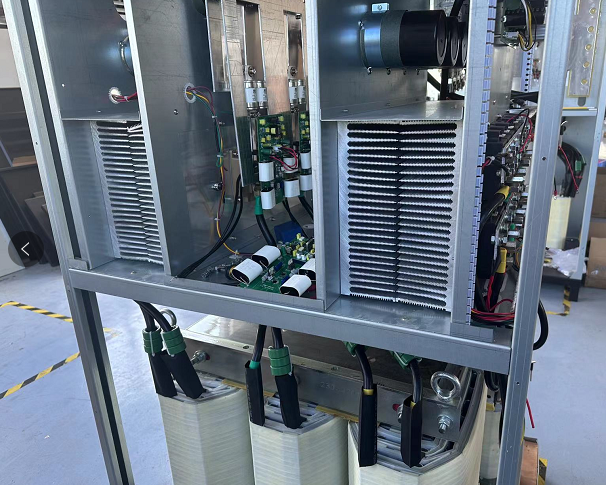
A typical UPS system consists of the following main components:
1.Inverter:
It converts DC power into AC power. In the event of a power outage, the inverter draws DC power from the battery and converts it into AC power required to supply the connected devices.
2.Battery:
It serves as the backup power source for the UPS, storing electrical energy. The battery is charged from the mains power when it is available and provides power when the mains power fails.
3.Charger: The charger is responsible for converting the mains power into charging current to replenish the UPS battery. The charger can adjust the charging speed and mode as needed to maintain the battery in good condition.
4.Static Switch: It monitors the status of the mains power and quickly switches to battery power when the mains power fails. The static switch ensures seamless power transfer to prevent any interruption to critical equipment.
5.Controller: The controller monitors the status of the mains power, battery charge level, and UPS operation. It may also provide remote monitoring and management capabilities through communication interfaces with other systems.
In addition to these primary components, a UPS may include filters, protective devices (such as overload protection, voltage regulators, and transient voltage suppressors), as well as display and alarm devices.
The operation of a UPS involves transferring mains power to connected devices while simultaneously charging the battery when the mains power is available. In the event of a power interruption or voltage irregularity, the UPS automatically switches to battery power and uses the inverter to convert the battery’s DC power into AC power for device supply.
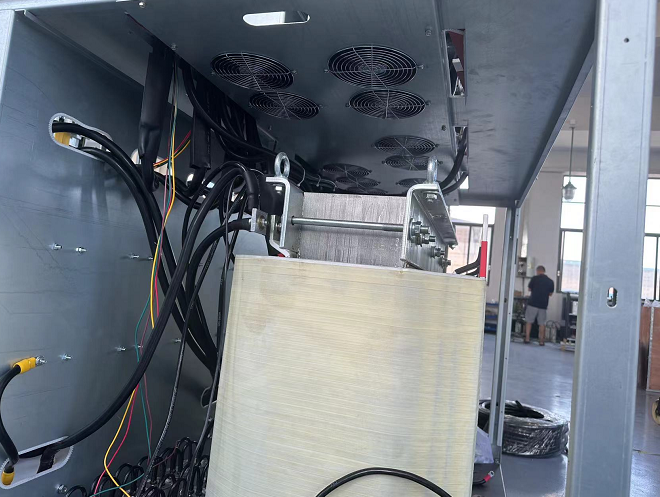
How to design a heat sink for UPS ?
Designing a heat sink for UPS (Uninterruptible Power Supply) involves considering factors such as the UPS power rating, thermal dissipation requirements, available space, and airflow conditions. Here are some steps to design a heat sink for UPS:
1.Determine thermal requirements:
Calculate the heat dissipation requirements for the UPS based on its power rating. This information is typically provided by the UPS manufacturer. Understand the maximum allowable operating temperature for the UPS components.
2.Assess available space: Evaluate the available space within the UPS enclosure for installing the heat sink. Consider the dimensions and shape of the heat sink that can fit within the given space constraints.
3.Select heat sink material: Choose an appropriate heat sink material based on its thermal conductivity and compatibility with the UPS components. Common materials include aluminum and copper, with copper offering higher thermal conductivity.
4.Determine heat sink size and shape: Consider the required surface area for heat dissipation. The size and shape of the heat sink will depend on factors such as the heat load, available space, and airflow conditions. Larger surface area and fin design can enhance heat dissipation.
Optimize fin design: Determine the optimal number, thickness, and spacing of fins on the heat sink. The fin design affects the heat transfer efficiency. Increasing the number of fins and reducing their thickness and spacing can improve heat dissipation.
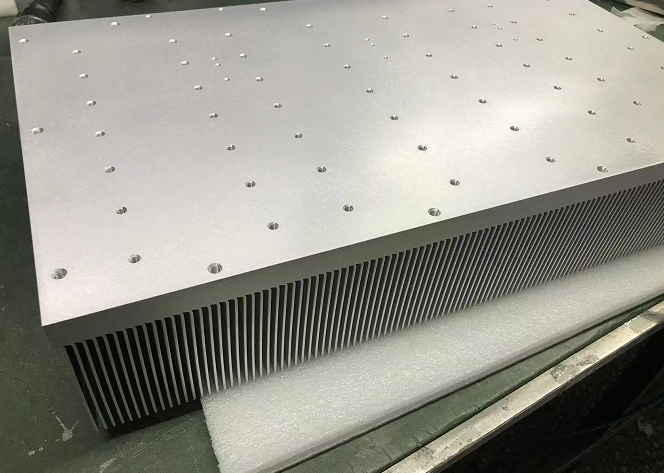
1.Calculate and optimize the heat sink parameters: Use thermal analysis software or equations to calculate the required heat sink parameters such as base thickness, fin height, fin thickness, and fin spacing. These parameters should be optimized to achieve the desired heat dissipation performance.
2.Enhance heat transfer:
Apply thermal interface materials (TIM) between the UPS components and the heat sink to improve heat transfer. TIMs such as thermal grease or thermal pads help fill in gaps and minimize thermal resistance between the surfaces.
3.Consider airflow management: Ensure proper airflow within the UPS enclosure to maximize heat dissipation. Incorporate fans or other ventilation systems to facilitate airflow through the heat sink and remove the heated air from the enclosure.
4.Prototype and test: Create a prototype of the heat sink design and conduct thermal testing to validate its performance. Measure the temperatures of the UPS components and assess whether the heat sink design meets the thermal requirements.
5.Iterative improvement: Based on the test results, refine the heat sink design if necessary. Consider adjustments to the size, shape, or materials used to optimize heat dissipation.
It is recommended to consult with thermal engineering experts or work closely with the UPS manufacturer to ensure an effective heat sink design tailored to the specific UPS model and operating conditions.
UPS systems find wide applications in environments where continuous and stable power supply is crucial, such as data centers, medical equipment, communication base stations, and critical manufacturing equipment. They protect equipment from power failures, voltage fluctuations, momentary power losses, and electromagnetic interference, ensuring uninterrupted operation of critical systems and data integrity.
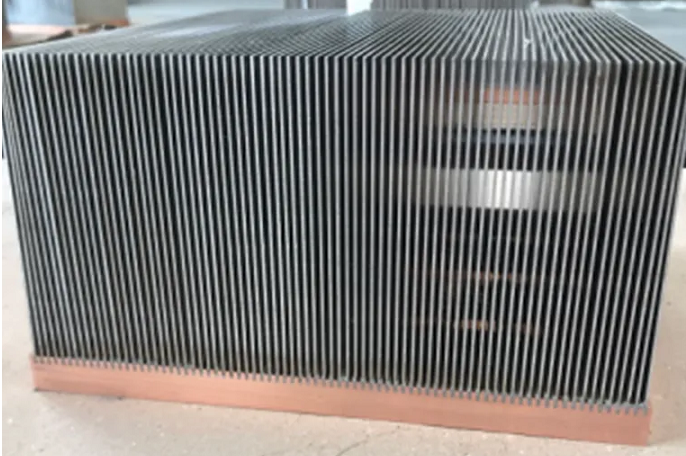