Importance of Helicoils in Heat Sink Assembly
Heat sinks are usually composed of components made of different materials such as copper1100, aluminum 6063,6061metals and Skived fin heat sink 1060 . At some critical connection points, such as mounting brackets and inlet/outlet connections, frequent assembly and disassembly operations may be required. Helicoil can be embedded into threaded holes made of softer materials (such as aluminum alloy) to form an inner thread with higher hardness and better wear resistance, thereby enhancing the strength of the threaded connection and ensuring that the threads in these areas are not easily damaged during repeated assembly and disassembly.
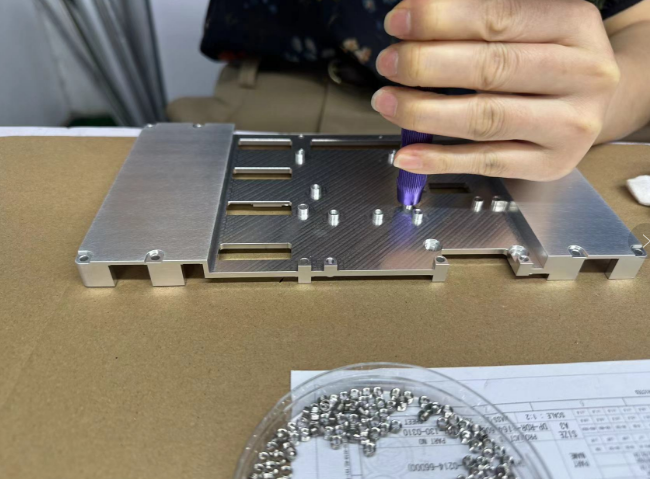
Compensating for Dimensional Deviations
During the manufacturing process of the heat sinks, due to limitations in the processing technology, there may be dimensional deviations in the threaded holes. Helicoil can compensate for this thread error to a certain extent, enabling fasteners (such as bolts and screws) to be screwed into the threaded holes more accurately and ensuring a tight connection between the various components of the heat sinks.Especially for lasers, precision components require M2 and M2.5 screws, so the properties of the material will limit the strength of the thread alignment. In this case, helicoils must be used to solve the problem.Similarly, for large IGBT modules, they need to be installed at the bottom of the heat sink.
Enhancing Assembly Strength for High Force Applications
Due to the high force required, ordinary threads cannot meet the requirements for fixed assembly. Usually, there are M5 and M6 screw holes. For aluminum or copper heat sinks, especially with the development of technology and the increasing demand for heat dissipation, more and more IGBT modules are using the skived fin heat sink process to dissipate heat. Its material is relatively soft aluminum 1060. Therefore, the importance of helicoil is self-evident.
Preventing Loosening from Temperature Changes and Vibration
The heat sink will be affected by factors such as temperature changes and vibration during operation. These factors may cause the threaded connections to loosen, which will then affect the normal operation of the heat sink. The special structure of Helicoil can increase the friction between the threads, effectively preventing the threads from loosening and improving the reliability of the heat sink structure.Specifically, some precision instruments and components must be installed on heat sinks with helicoils to prevent screw loosening during transportation. For example, high-power liquid cooled plates usually handle a large amount of heat, and high-power components are often fixed on the liquid cooled plates.
The heat sinks may come into contact with cooling fluids, moist air and other media with a certain degree of corrosiveness. Helicoil is usually made of corrosion - resistant materials (such as stainless steel). After it is embedded into the threaded hole, it can provide a corrosion - resistant protective barrier for the thread, reducing the possibility of the thread being corroded and extending the service life of the heat sinks.
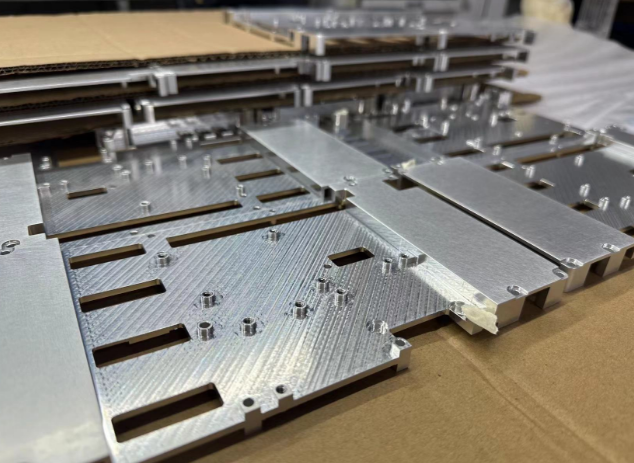
Applications Beyond Heat Sinks
The application field of helicoil is relatively wide, in addition to heat sinks, there are other fields. In the aerospace industry and spacecraft manufacturing, there is a high requirement for lightweight, while also bearing various stresses in launch and space environments. helicoil can improve the strength and stability of threaded connections under limited weight, such as in the assembly of satellite structures and the installation of various precision instruments.
In the automotive industry, the engine, as a core component, generates vibration during operation. helicoils can effectively prevent the loosening of threaded connections in engine cylinder blocks, cylinder heads, and other parts, improving the reliability and durability of the engine.
For mold manufacturing, molds need to be frequently loaded, unloaded, and debugged. helicoil can improve the durability of mold threaded holes and reduce mold maintenance and replacement costs caused by thread wear.
KENFA TECH's Use of Helicoils
KENFA TECH generally uses imported Helicoils for the installation of customers' products. These high-quality and high-precision products can provide reliable guarantees for customers' products. Generally, we use Helicoils with specifications such as 2-56, 4-40, 8-32, etc., and the brand selection is also KATO.
