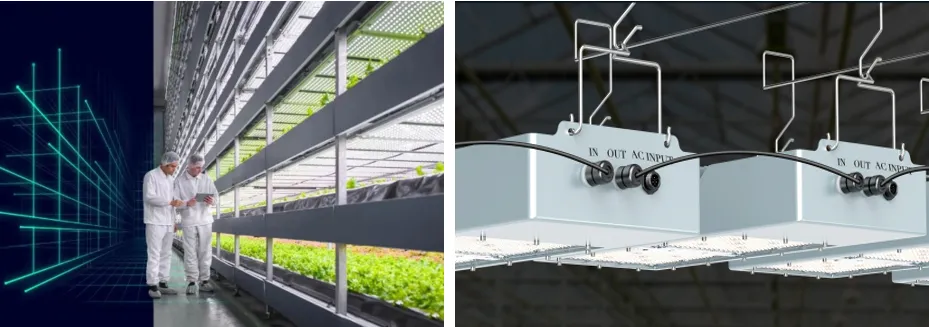
The high-power skived fin heat sink is used in LED plant lighting for vertical agriculture.By implementing vertical farming methods, farmland water use per square meter of crop yield has been reduced by 95%, crop yield has been increased by 300 times, and production efficiency and scale have been significantly improved.
Compared with traditional greenhouses, vertical agriculture can accurately judge the indicators in the environment of the plant, monitor the growth environment of the plant 24/7, and use LED lights to control the amount of light received by the plant. At the same time, the temperature, humidity, carbon dioxide content in the air and nutrient content in the soil are controlled by manual intervention to create favorable conditions for the growth of plants.
The importance of LED plant lights
With the acceleration of urbanization, food security is facing great challenges. As an advanced stage of the development of modern facility agriculture, vertical agriculture is not affected by climate, season, location and geographical conditions, does not require the use of farmland, high space utilization, can be 365 days a year, 24 hours a day uninterrupted cultivation of crops and other advantages, has a very considerable application prospects and potential. The development of vertical agriculture with double production capacity may become a new solution to ensure national food security and the only way for sustainable human development.
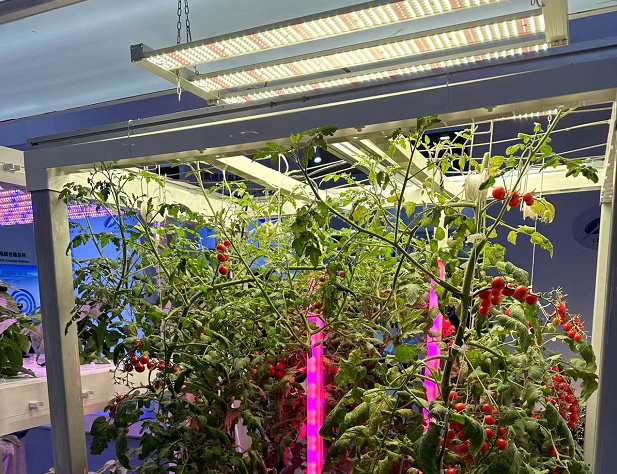
The role of heat sink in LED grow light lamps
The use of high-power skived fin heat sink is conducive to the heat dissipation of LED chip, reduce the light attenuation of LED, and improve the light efficiency of LED.The main function is to conduct and dissipate the heat generated in the LED plant lamps rapidly by means of heat conduction and heat dissipation, so as to maintain the working temperature of the lamps within a reasonable range. Radiators are usually made of AL1050 materials with high thermal conductivity, which are able to effectively absorb and conduct heat so that heat can be evenly distributed to the surface of the heat sink.
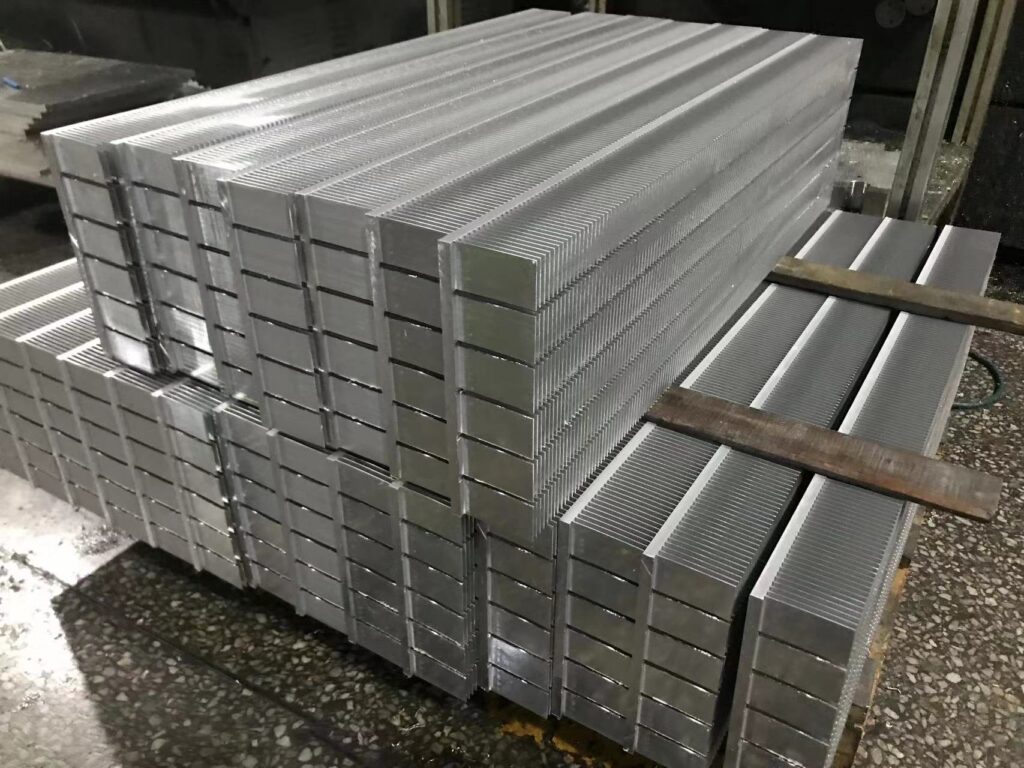
Making the skived fin heat sink of the standard specifications
Materials: Copper C1100, Aluminum6063/1060
Aluminum:
- Flow Length: 700 mm MAX
- Width: 2000 mm MAX
- Fin Thicknesses: 0.2 – 2.5 mm
- Fin Height: 130 mm MAX
- Fin Gap: 1:1.2 to 1:8 fin thickness to fin gap ratio
- Copper:
- Flow Length: 120 mm MAX
- Width: 600 mm MAX
- Fin Thicknesses: 0.05 – 1.2mm
- Fin Height: 0.6 – 60 mm
- Fin Gap: 0.05 MIN
General Guidelines: - Aluminum is better for higher aspect ratios
- Airflow lengths limited by cutter and the force
required to fold up fins - Most dimension variables have a tradeoff
with other design variables - The low end of the fin thickness range shown
would be for shorter fin heights only
The skived fin heat sink benefits for cooling chipsets
- Higher Efficiency Cooling & Better Performance
- Thin Fin & High Fin Density Capabilities
- Lower Tooling Cost
- Economical Copper Fabrication
- There is no thermal resistance between the bottom plate and fins, in contrast to solder paste soldering, epoxy resin bonding and brazing processes
If you want to make a skived fin heat sink, you should thinking the following:
- Are you using Natural or Forced Convection for cooling your chipsets?
- How do you assembly your heat sink?
- What is the maximum ambient temperature that your
device will be operating in? - How much power is your device dissipating?
- What is your maximum device case temperature?
- How much room do you have for your heat sink?
- Does the production cycle of 2 weeks meet your time requirement?
- Do you have a large demand? Whether to consider using the profile process or continue to use the skived fin process.