

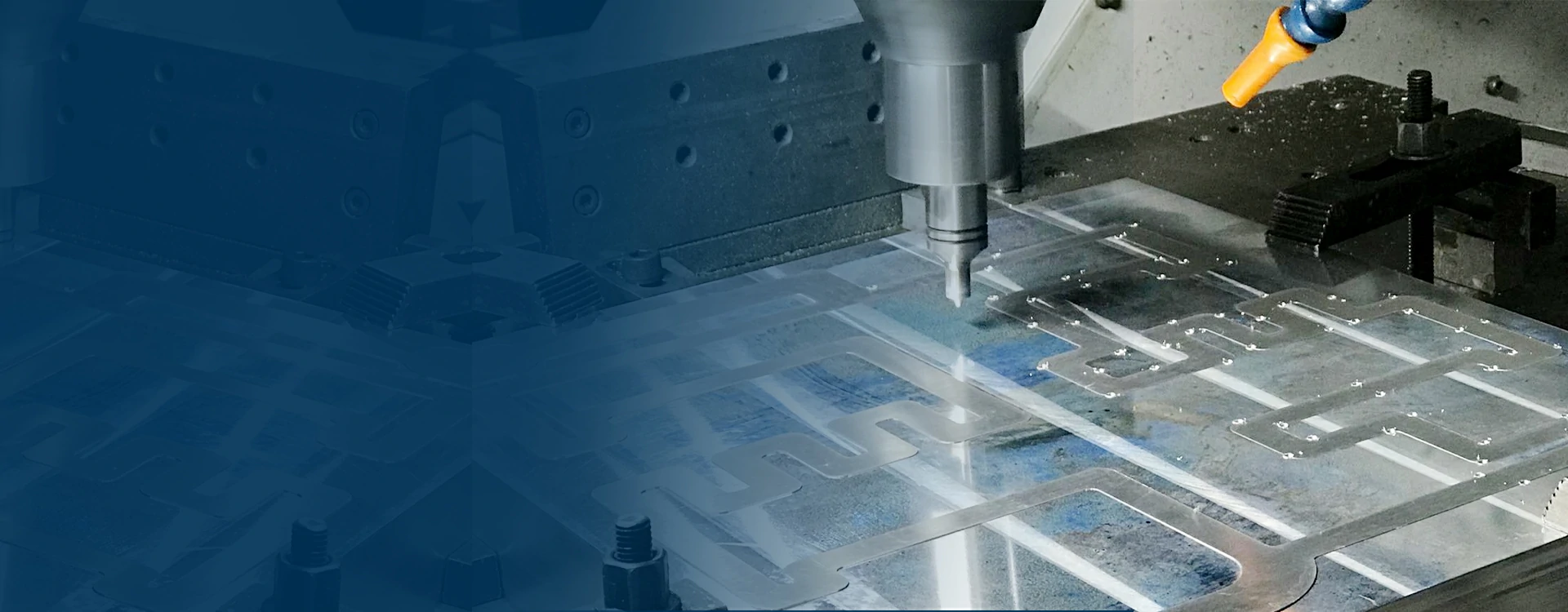
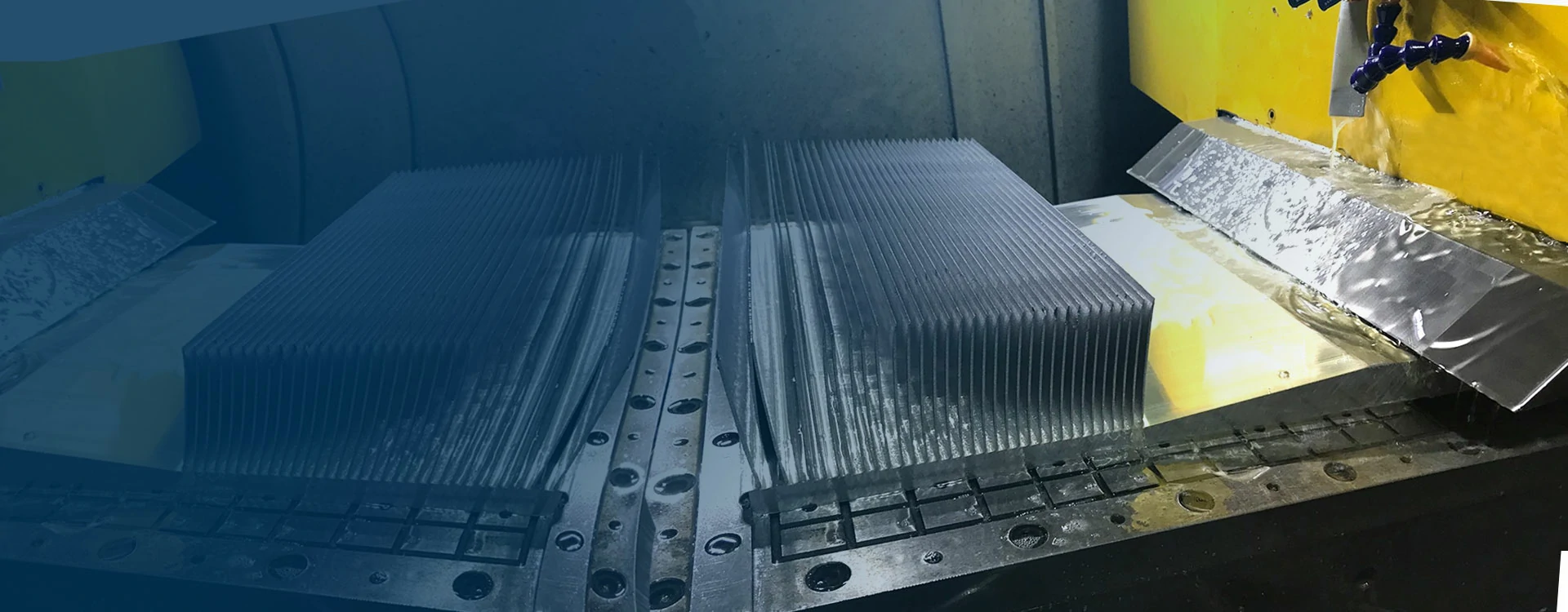
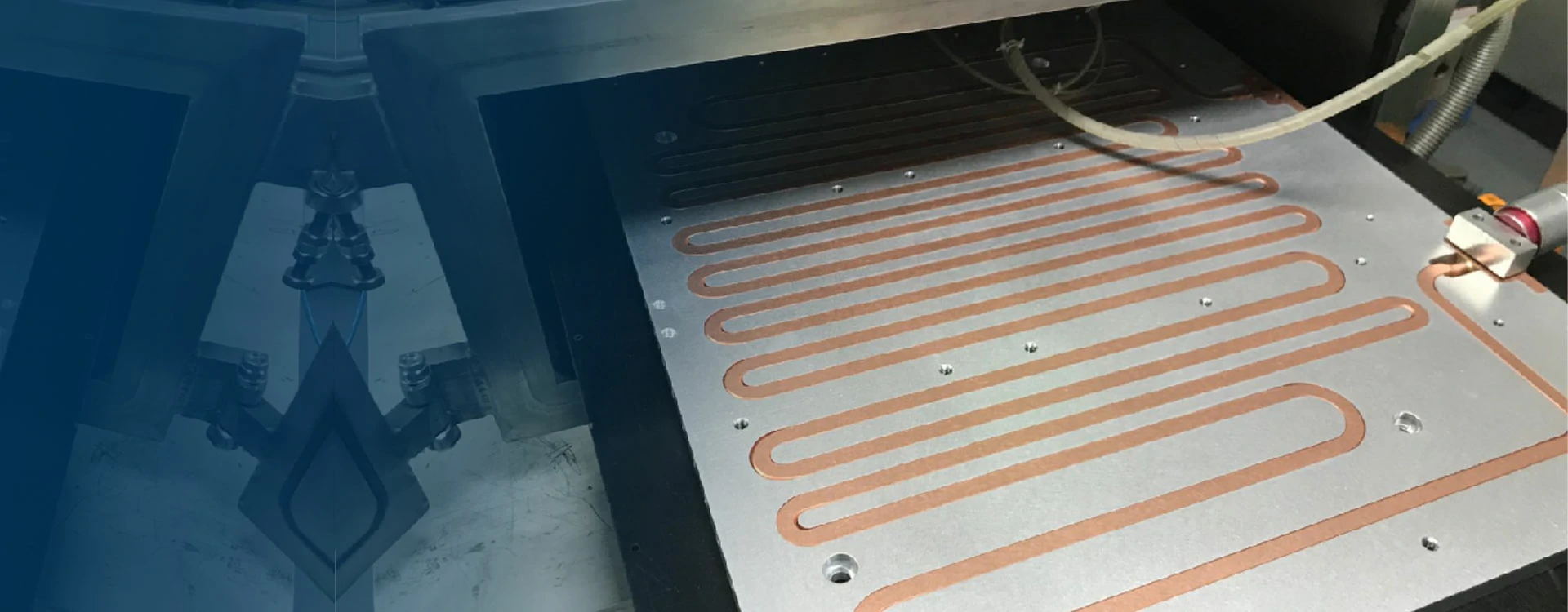
with over 10 years of experience
A reliable production process is the guarantee of quality.
Customized Design And Manufacturing
Customized Design And Manufacturing
Customized Design And Manufacturing
Customized Design And Manufacturing

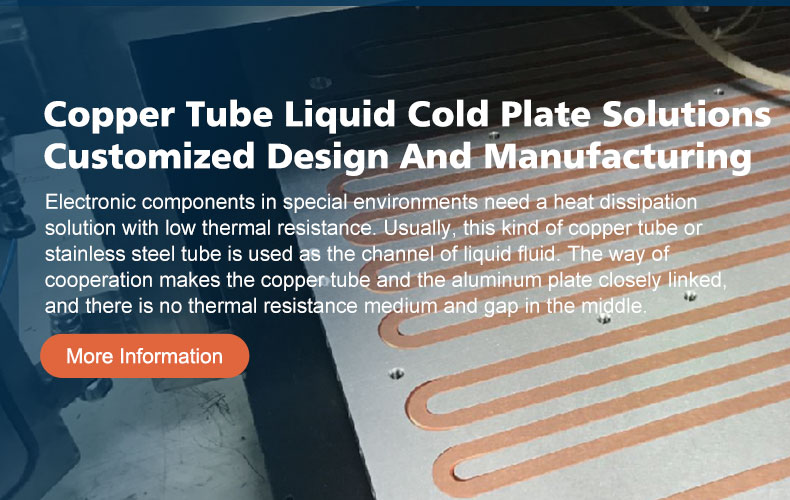
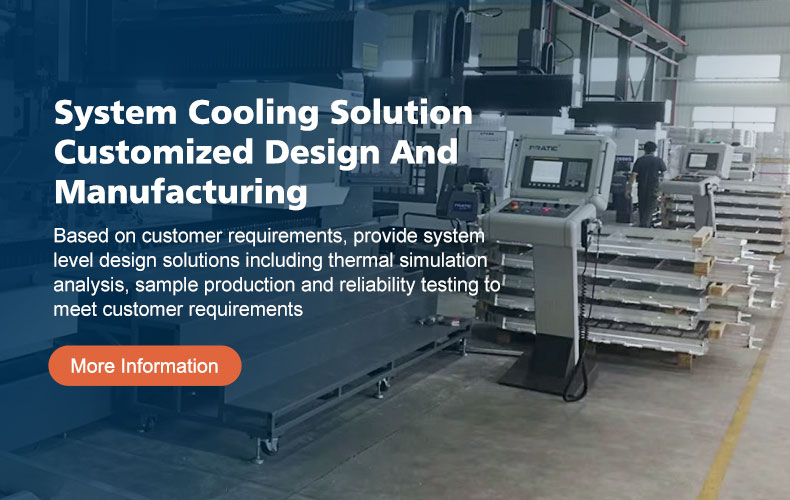
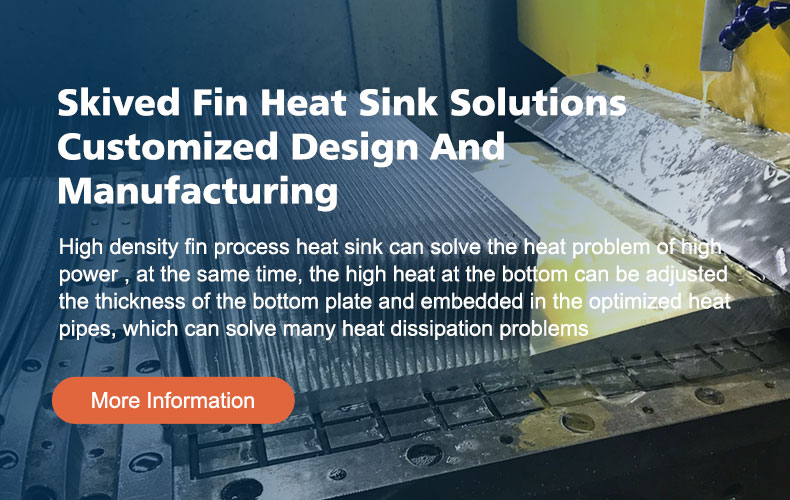
Heat Sink and Liquid Cold Plate Manufacturing Services
Kenfa Tech, a distinguished high – tech enterprise, excels in the comprehensive process of high – power heat sink and liquid cold plate production, including meticulous design, advanced development, rigorous testing, precise optimization, and customized manufacturing. Our team of experts, armed with cutting – edge technology and extensive experience, ensures that each heat sink not only meets but exceeds industry standards. We are dedicated to providing customers with top – quality products of unwavering reliability and the most economically efficient design solutions, making us a leader in the heat sink technology domain.
Kenfa Tech is a total thermal solution design and production company, providing customers with the best cooling solutions for different needs.It is also most cost-effective solution.






Kenfa Tech Industrial Limited, a national high-tech enterprise with over a decade of experience, specializes in heat sinks production. We offer diverse cooling solutions tailored to market demands. Our skilled engineers, formerly with renowned cooling firms like AAVID and Foxconn, ensure precise project control and seamless product development.
Utilizing Ansys Icpak and Flothermal software, we conduct thermal analyses for customer engineers. Our structural engineers optimize production processes following sample testing, delivering cost-effective solutions. Our comprehensive production line includes CNC precision machining, high-power heat sink soldering, skived fin heat dissipation, brazing process, friction stir welding, flow resistance of liquid cold plates and rigorous testing methods. We also provide surface treatments like cleaning, degreasing, and chromate coating. Accredited with ISO9001:2008, ISO14001:2004, and IATS16949 certifications, we assure customers of system-level quality standards.
Our robust capabilities go beyond numbers.
How to serve our customers
With our more than 10 years of production and operation, we can quickly respond to customer needs, streamline and accurately control the entire production cycle of products, at the same time, based on our ERP system, we generally follow four steps to complete

Get the customer's needs
We usually get some heat sinks or cooling system design requirements from our customers

Design or DFM
After receiving the drawings of existing designs, our engineers will conduct a DFM evaluation. In addition, for some customer-oriented conceptual designs, our engineers are required to perform structural design and thermal protection analysis.

Making Samples
After getting the customer's confirmation of the drawing, we will arrange the production of the sample, which usually takes 3-4 weeks to complete according to the customer's payment date
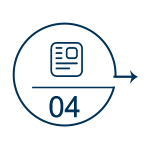
Customer Confirmation
After the customer's test, finally determine whether to meet the requirements
Our advantages
We have more than 10 years in the heat sink production and processing of advantages, R & D design team for customers to do the thermal solution and design programs, quality systems and process specifications.
– OEM/ODM for customers.
– Lead time 3 to 4 weeks.
– ERP system control process.
– ISO9001:2015 Certified Factory
– IATF 16949:2016
– More than 10 years making heat sinks experience.
– Professional thermal analysis software (Icepak,Ansys,Qfin )
– Engineer 1 to 1 project management and technical support.
– Reliable after-sales service
Main Production Manufacturing Equipments
For heat sink production equipment, different process products need different equipment, relatively speaking, high-power products will basically use CNC machine , soldering welding furnace, friction stir welding machine, skived fin machine and so on
Our Latest Blog Posts
Check our latest blog posts, you can know the latest situation of our company, especially the new technology and new technology, can have a certain design inspiration for the customer design engineers
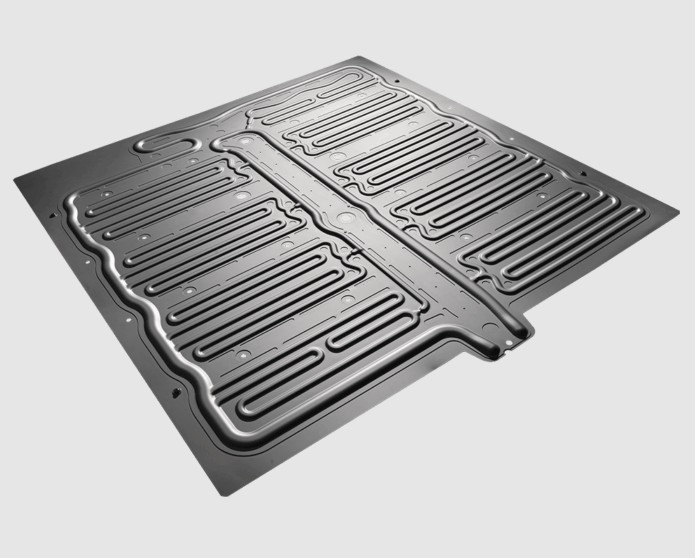
How Are Battery Cooling Plates Made?
Introduction Battery cooling plates are essential components in the thermal management systems of batteries, particularly in electric vehicles (EVs) and energy storage systems. Adequate cooling is crucial to maintain battery performance, safety, and longevity. As demand for efficient energy solutions grows, understanding the manufacturing process of these plates becomes increasingly
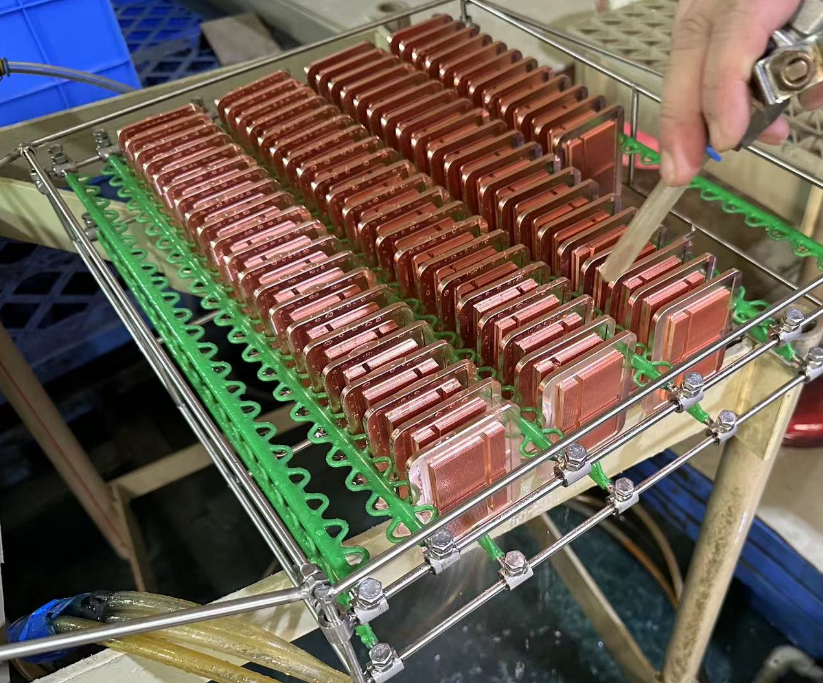
Copper Liquid Cooling Plate VS Aluminum Liquid Cooling Plate
Liquid cooling plates are integral to many cooling systems, serving as vital components for effective heat dissipation. When choosing a liquid cooling plate for your system, there is a significant difference between copper and aluminium materials. Each material has unique benefits and drawbacks that users should carefully examine. This book
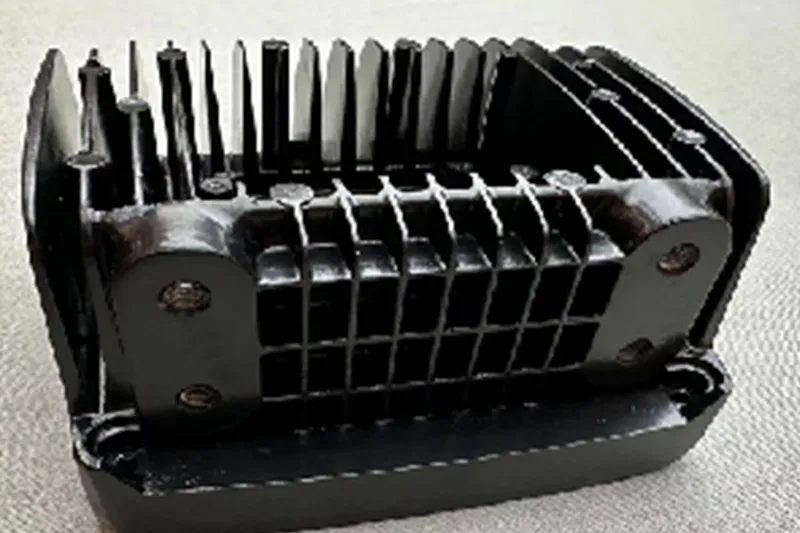
How are AI advancements impacting heat-sink technologies and market trends?
Introduction The heat sink industry, an industry that was not focused on in the past, is gradually moving from behind the scenes to the front of the stage due to the explosive growth in the amount of data and computation brought about by AI. China’s Data Center Power Density Increases
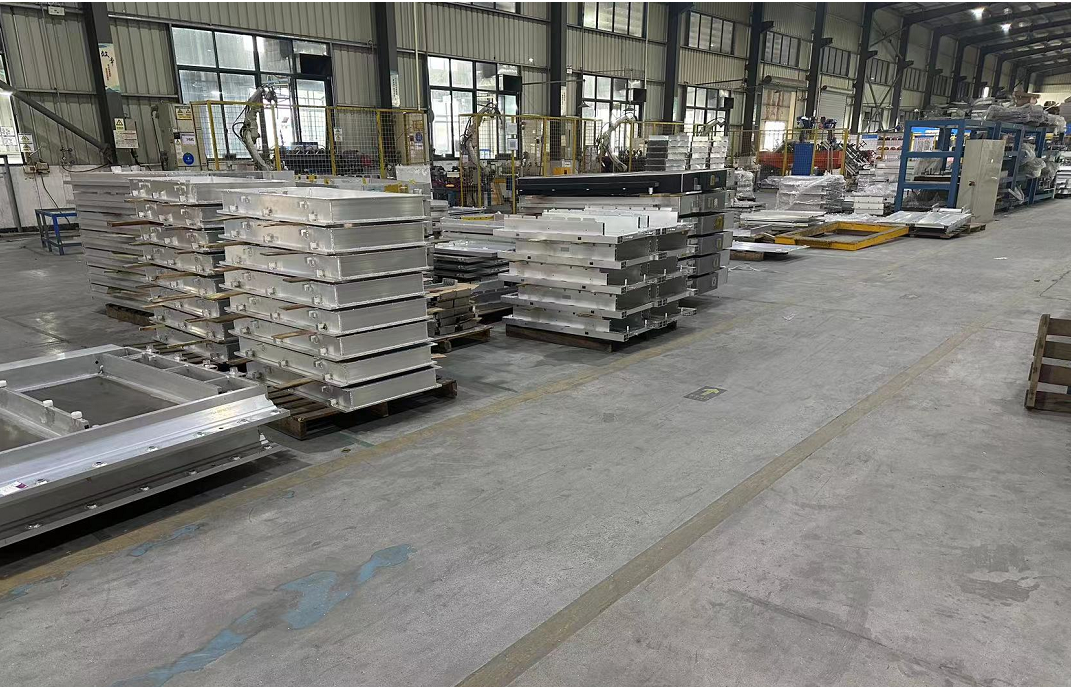
What is an Electric Vehicle liquid cold plate?
With the rapid development of the electric vehicle industry, the use of pure electric vehicles has become increasingly common. During the normal operation of a car, lithium batteries generate a lot of heat. To ensure the safe operation of lithium batteries, it is necessary to carry out thermal management on