Liquid Cold Plates Manufacturer
How to choose a suitable liquid cooling plates for your project depends on the chip's heating power, as well as the corresponding size ,making process and material. These are all system level design solutions. Perhaps, we are the system level design supplier for the cooling field that you just need.
Liquid Cold Plates
Kenfatech is a leading liquid cold plates manufacturer offering custom solutions for high-performance thermal management. Our factory in China specializes in liquid cold plates, heatsinks, and advanced heat dissipation products designed to meet the rigorous demands of industries like automotive, 5G communication, and cloud computing.
We provide high-thermal-conductivity solutions tailored to your specific needs, ensuring optimal heat dissipation in critical applications. Our products are engineered to support high-pressure environments, demanding operational conditions, and complex designs.
Liquid cold plates are an essential component in high-tech industries. Their efficient cooling capabilities ensure the reliability and performance of systems such as electric vehicles, telecommunications equipment, and cloud servers.
Friction Stir Welded (FSW) Liquid Cold Plates from Kenfatech leverage advanced welding technology for superior thermal performance.
Engineered for superior heat transfer, our brazing liquid cold plates promise exceptional reliability.
Offering robust cooling solutions, our extruded liquid cold plates cater to high-performance applications.
Experience superior thermal conductivity with our copper tube liquid cold plates, ideal for high-load cooling tasks.
Designed for complex cooling needs, our drilling liquid cold plates provide unmatched heat dissipation efficiency.
The aluminum extrusion of the harmonica tube process, through argon arc welding and laser welding, can provide efficient and low-cost cooling solutions for the battery pack module
All You Need To Know About Liquid Cold Plates
Liquid cold plates are critical components used to manage heat in advanced technologies. They consist of a thermally conductive base, often copper or aluminum, through which coolant flows to remove excess heat. These systems are known for their ability to handle high heat loads, making them indispensable in industries such as automotive, telecommunications, and cloud computing.
These cold plates are typically used in applications where traditional heatsinks or air-cooling solutions are insufficient. They provide efficient and compact thermal solutions for high-performance systems that require reliable, long-term heat management.
Custom Liquid Cold Plates for Different Industries
We focus on providing customized liquid cooling plate solutions, serving multiple industry fields. With professional technology and rich experience, we deeply understand the characteristics of heat dissipation requirements in different industries, ranging from electronic technology to mechanical manufacturing, from energy and power to the automotive industry, etc. We conduct precise designs to ensure that the water cooling plates perfectly match various devices and achieve efficient heat dissipation. High-quality materials and exquisite craftsmanship are adopted, and quality is strictly controlled. We offer one-stop services from conceptual design to finished product delivery, safeguarding the stable operation of your equipment, helping different industries overcome heat dissipation problems and realize performance optimization and efficient development.
Key Considerations When Choosing Liquid Cold Plates
When selecting liquid cold plates, there are several important factors to consider to ensure optimal performance:
Fluid Compatibility
Choosing the right coolant for your application is crucial. The coolant must be compatible with the materials of the cold plate and provide efficient heat transfer without causing corrosion or degradation of components.
Thermal Requirements
Understanding your system’s thermal load and the required cooling capacity is key to choosing the right cold plate. We provide custom solutions based on your specific temperature control needs.
System Integration
The design of the cold plate must match the physical constraints of your system. We offer tailored designs to ensure seamless integration with your application.
Material Selection
The choice of materials for the base plate and other components is essential for maximizing thermal conductivity and corrosion resistance, especially in demanding environments.
Reliability and Durability
Our liquid cold plates are designed for long-term reliability, with an emphasis on durability under high-pressure, high-temperature conditions. We ensure that our products meet the toughest industrial standards.
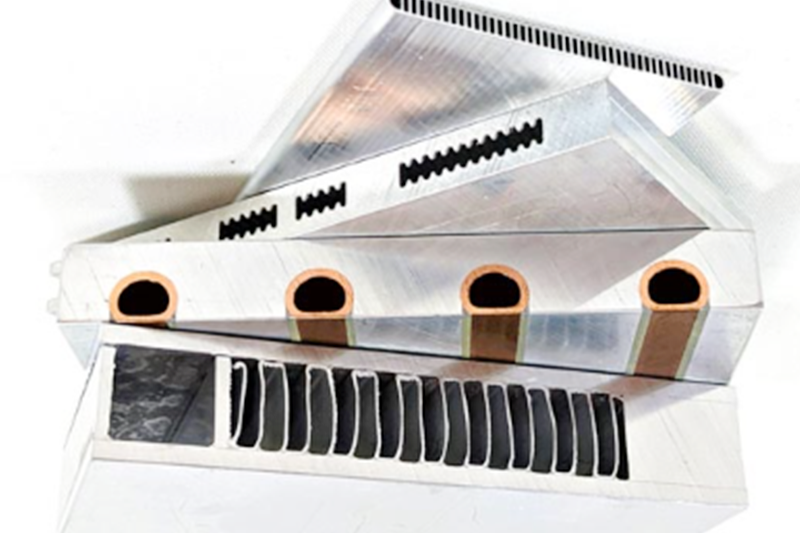

How to Test the Leakage of the Cold Plate?
The reliability of the cold plate is a very important evaluation parameter in the entire product attribute. Usually, the working pressure of the customer’s water pump or circulation system is around 0.2-1.0Mpa. Therefore, when testing the cold plate, we first need to clean the flow channel of the cold plate with a water temperature of 80 degrees Celsius to prevent oil stains and aluminum cutting from entering the circulation cooling system.
Then put the cleaned cold plate into the testing platform. At this time, we can connect the inlet and outlet of the cold plate through a 1.5Mpa air pressure to ensure that the air pressure is fully filled in a closed circulating flow channel. This pressure holding time is usually 5-20 minutes, depending on the customer’s needs and actual application conditions. Usually, we do a 10 minute pressure holding test to determine if there is any leakage.
After completing the pressure maintaining test, we will enter another stage of testing the flow resistance, which is also very important because we will analyze it through simulation software during the design process to obtain a theoretical flow resistance parameter that needs to be matched with the water pump and circulation system used by the customer’s time. Adding excessive flow resistance will increase the load capacity of the water pump, and we will also note that, If there are impurities or aluminum cutting residues inside the flow channel during the processing, we can select this unqualified cold plate through data comparison.

Air pressure holding test

Flow resistance test

Helium leak test
How We Help Customers Design Liquid Cold Plates
We help customers optimize liquid cold plate designs through thermal simulation, saving time and costs. If customers lack design expertise, we offer free custom solutions, reducing development time by 30% and R&D costs by 50%. Here’s what we need to get started.
-Size:
Provide the ideal dimensions (e.g., 200x200x15mm) based on your cabinet size for a custom cooling plate design.
-Material:
Choose materials like aluminum for weight and cost, or copper/stainless steel for corrosion resistance in specific environments.
-Thermal power:
Share the chip’s power and PCB position, allowing us to design tailored flow and microchannels for effective cooling.
-Environment temperature:
Inform us of the operating environment temperature (typically 35-45°C) for accurate simulation settings and heat management.
Temperature and flow rate of liquid inlet:
Specify liquid inlet temperature and flow rate to optimize cooling channels for the best heat transfer efficiency.


Why Choose Kenfatech's Liquid Cold Plate?
Design and Development Expertise
Our team's proficiency in creating tailored liquid cold plate solutions sets us apart. We harness our deep understanding of thermal dynamics to design products that meet your specific needs.
Quality Assurance
We implement stringent quality control measures, ensuring the reliability and durability of our products. Our liquid cold plates stand the test of time, providing a robust solution for your cooling needs.
Wide Product Range
From FSW to brazing, extrusion, and copper tube liquid cold plates, we offer a diverse product range, catering to various industry applications and power densities.
Timely Delivery
We understand the importance of time in business. Our efficient production management protocols ensure we deliver high-quality products right when you need them.
Customer Service
Our commitment extends beyond product delivery. We provide exceptional customer support, assisting you at every step of your journey with us. deliver high-quality products right when you need them.
Proven Track Record
Our track record of successful collaborations across various industries speaks volumes. Companies worldwide trust Kenfatech to provide them with top-notch thermal management solutions.
Sharing Some Case designs
Our thermal design experts will use Ansys Icepak thermal analysis software to design the heat sinks, liquid cold plate solutions for customers, to realize the initial theoretical feasibility, and then move to the actual sample production, which will save the cost and development cycle for customers.We share that these case designs were independently developed and designed, and all intellectual property belongs to Kenfa, which is also a part of trade secrets.At the same time, when designing liquid cooled plates, the design and optimization of microchannels will also be considered.
1,How to optimize the microchannel design of liquid cold plates
2,Design and Optimization of Flow Channels for Liquid Cooled Plates
3, Slection of coolant for liquid cold systems
4, How can I tell the pros and cons of a liquid cold plate design
5, How are battery cooling plates made?
6, Copper liquid cold plate vs aluminum liquid cooling plates
7, What is an electric vehicle liquid cold plate?
8,How to avoid the occurence of leakage in the design process of the liquid cold plate?