Thermal Management of EMobility
The thermal management of the battery cell is a very important part of the entire electric vehicle system, providing range and power support for the vehicle's power
EV Battery Liquid Cold Plate
The core components of electric vehicles are lithium batteries or lithium-iron phosphate batteries. These battery modules are arranged regularly and designed in different parallel and series ways according to current and voltage requirements. When the battery needs to be charged, the electrons inside will move, which will generate a large amount of heat. Some batteries will have a fast charging mode, during which the heat will accumulate more, but when charging slowly, it will have relatively low heat. An excellent thermal management system can ensure a stable range of electric vehicles. The high-performance liquid cooling plate manufactured by Kenfa can be used well in this thermal management system. The stamping brazing cold plate, profile process cold plate, and friction stir welding cold plate are all perfect solutions. So, the thermal runaway problem of the battery module can be avoided under our system-level thermal management.
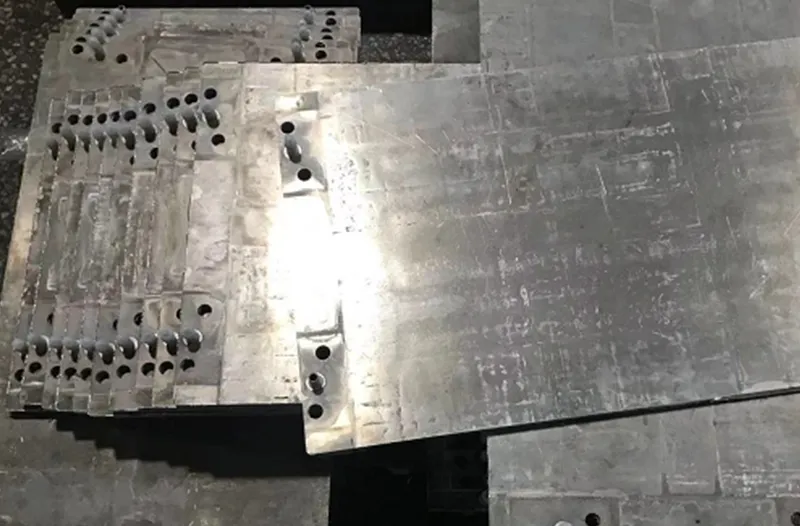

Liquid Cold Plates Control The Thermal Runaway of EV Batteries Cells
The role of liquid cooling plates in the thermal management of electric vehicle batteries mainly stems from their efficient heat conduction and dissipation characteristics. Electric vehicle batteries generate a lot of heat during charging and discharging. If effective heat dissipation is not achieved, it may lead to temperature rise and thermal runaway, ultimately affecting battery performance and lifespan. The liquid cooling plate conducts the coolant to the battery module through the built-in thermal conductivity pipeline, absorbing the heat generated during the battery cooling process. Subsequently, the coolant carries the heat to the surface of the liquid cooling plate and effectively dissipates the heat energy to the surrounding environment through radiation, convection, and heat conduction. This cooling method can maintain the battery temperature within an appropriate range and prevent thermal runaway caused by overheating. Therefore, liquid cooling plates have become an essential thermal management technology in electric vehicles, ensuring battery systems’ stability, safety, and performance.
Inverters Liquid Cold Plates
Electric vehicles’ internal power supply system is composed of many electronic components, and the voltage used to operate these components is usually AC. At this time, our battery has DC voltage, so we need to convert this DC voltage into AC voltage to meet the needs of the components. Similarly, many components are DC, but the voltage requirements are different. Under such conversion conditions, a large amount of heat will be generated. To accurately control the voltage of these components, it is necessary to maintain the temperature of the components. A sound heat dissipation system and heat sink are essential at this time. We usually use a liquid-cooled plate system to control the temperature of the components. Usually, these inverters are wrapped in a metal cavity, and many components must be sealed to prevent water from entering; we will design a liquid cooling plate with die-casting technology to complete heat dissipation.
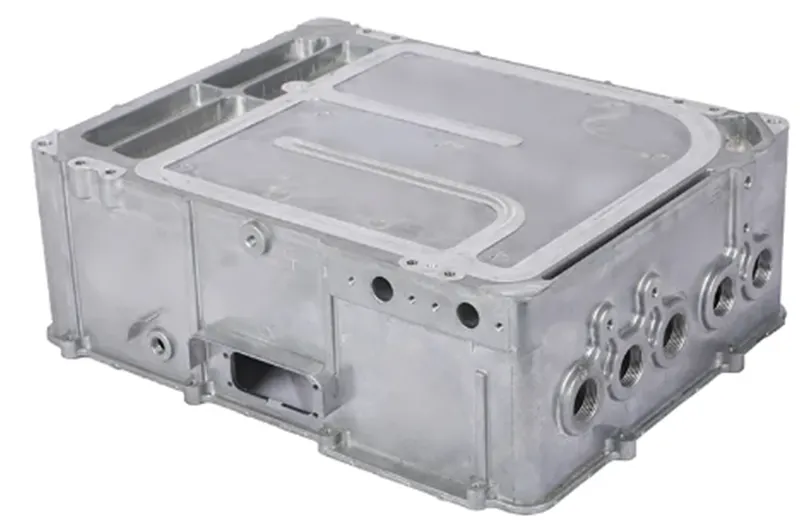

The Cold Plates For Autonomous Driving of Automobiles
With the emergence of the autonomous driving function in automobiles, the auxiliary driving function is becoming increasingly important. With the improvement of multi-level chip computing and computing speed, a cooling system is needed to manage the heat generated by high-speed operation and computing to support complex situations that occur during the autonomous driving process, make correct judgments, and respond promptly. We have over ten years of production experience in providing customers with liquid-cooled plate solutions to solve this problem. Usually, we use CNC machined cavities and design many flow channels inside. The entire system is closed, ensuring the stable operation of this autonomous driving component with a fixed flow rate input.


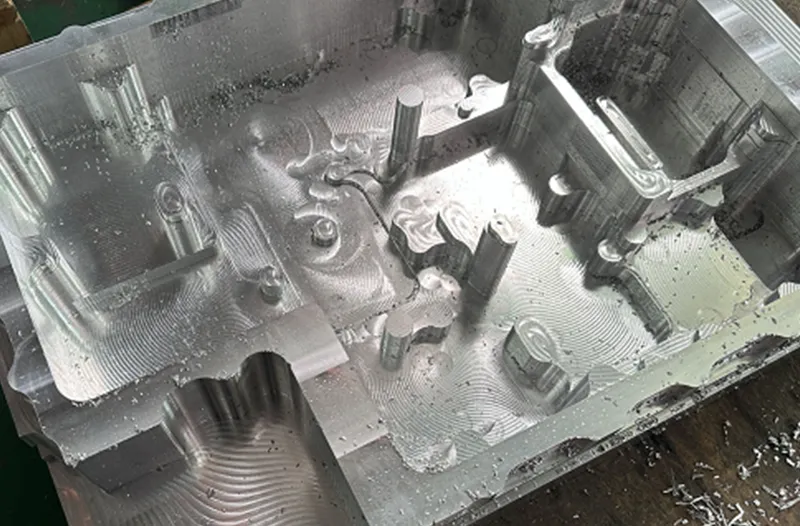
Why You Choose to Cooperate With Us.
We adopt the liquid cold plate system scheme, which can help you design and solve the problem of battery cells heat dissipation problem with higher power density. Of course, our cold plate is light in weight, safe, and reliable, and the water nozzle with various interfaces can meet the connection of different tubes. The brazing cold plate or profile process cold plate can bear the weight of the battery. We use the structure and material to optimize and strengthen the structure of the cooling system of the battery cells.
Our engineers design optimized cold plate systems that help optimize the temperature control of power inverters and converters to maximize energy conversion efficiency, energy use, and distribution to energy storage systems and EV batteries for stable operation.
Considering the battery installation process, we streamline the design structure for customers to meet the design solution’s low cost and high efficiency. Of course, we will also communicate with customers in the design process, the sealing of the cold plate, and the choice of liquid corrosion of the cold plate wall; because the area of the cold plate is relatively large, flatness is also an important parameter to consider.
Problems Encountered During Battery Operation
Electric vehicle batteries need to be tested in extreme conditions for years. They must achieve the most efficient extension of safe and reliable battery performance, prevent extremely high temperature, cold, UV exposure, wind, sand, rain, road vibration, and sudden impact, have high battery cell strength, protect the battery from rain, sand, and dust invasion or corrosion, and Maximize the battery life.
Therefore, any energy storage battery system or cooling system can contact us; our professional design level and reliable manufacturing level can meet your needs; in a word, the reliability of the battery system is a severe thing and must put safety and reliability in the first place, so the thermal management program is essential to opt the liquid cold plate system scheme can help you design and solve the problem of battery cells heat dissipation with.
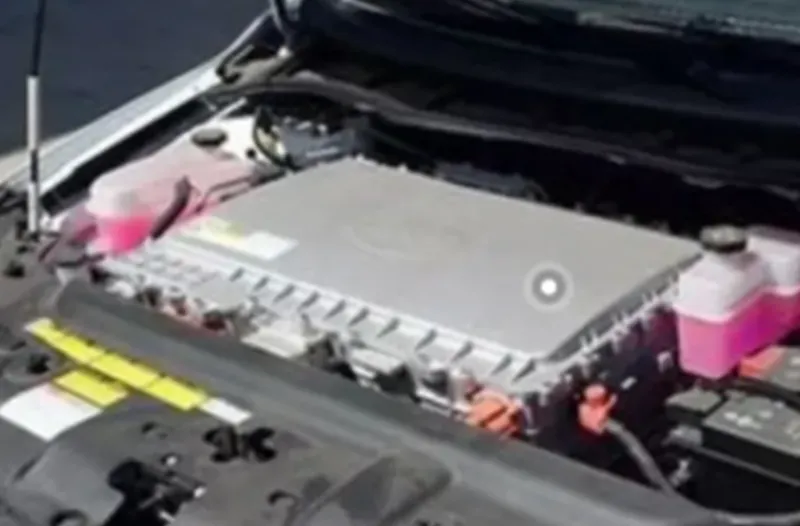

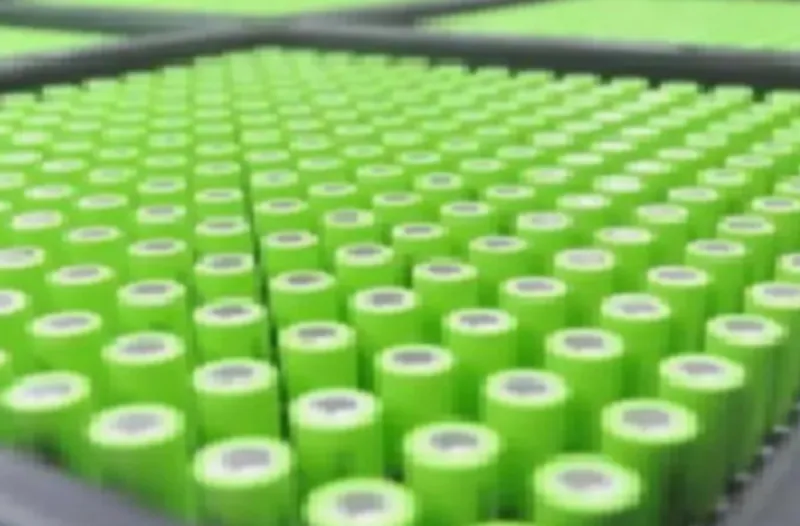
Our standard liquid cold plate products for battery cells coolin
Based on our more than ten years of production experience, we have summarized many case studies of customer needs and found that the module specifications of many battery cells are universal, and the different changes are the series-parallel method to change the current and voltage. Therefore, we have designed some standard liquid cooling plates with solid universality, and the molds are our patent rights, providing customers with quick sampling for testing and shortening the development cycle of engineers.
Paper on battery cooling scheme.
The thermal management of batteries is based on the influence of temperature on the battery, combined with the chemical characteristics and heating principle of the battery, and based on the specific optimal charging and discharging temperature range of the battery through reasonable design and establishment of scientific, electrochemical, heat transfer, and molecular dynamics research, as well as research on new materials and production processes of heat sinks, to solve the heat dissipation and thermal runaway problems caused by high or low temperature (low temperature) conditions of the battery, and improve the overall performance of the battery. KENFA technology shares some articles based on years of production and design experience, which can provide some design references for engineers.
What is the heat transfer in an EV battery?
What is the difference between a heat sink and a cold plate?
How do you design a heat sink for an EV battery?
How do you design a liquid cold plate for an EV Battery?