Round Tube Liquid Cold
Plate
Our professional thermal design engineers have designed a number of standard tube liquid cold plates. You can check the parameters and choose the right size liquid cooling plate for your project.
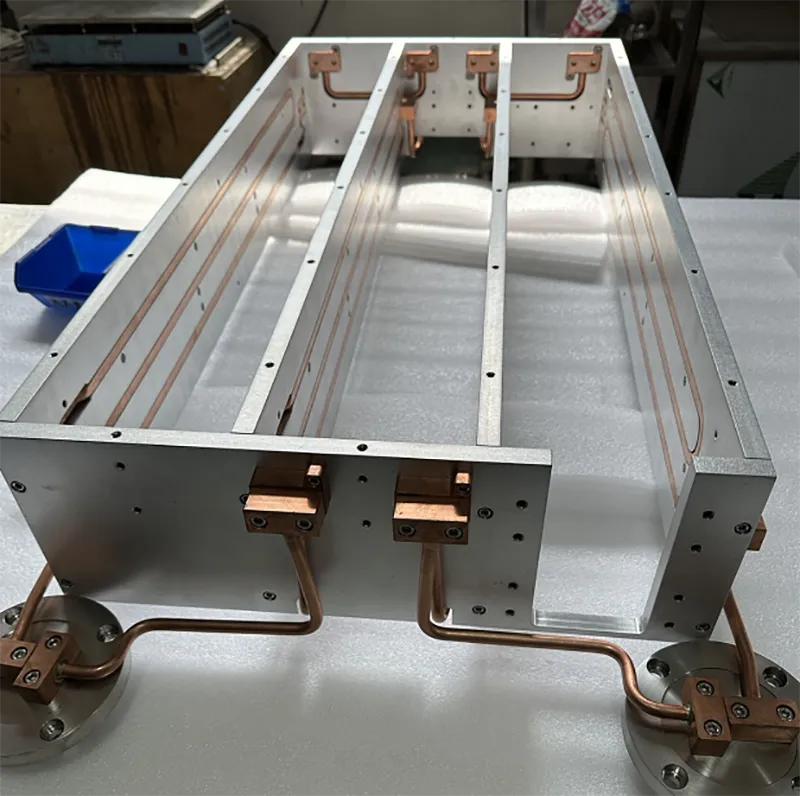
What Is A Tube Liquid Cold Plate?
The liquid cooling plates of circular tubes can generally be divided into two types: stainless steel tubes and copper tubes. The circular tubes used for liquid cooling plates serve as flow channels.Tube cold plate technology optimizes the contact area with the cooling surface. By adjusting the distance between copper tubes, the desired length and area of the waterway can be obtained to ensure that enough liquid passes under the heat source to take away a large amount of heat.
To provide optimal thermal performance of the liquid cooled plate. Our engineers have calculated the mechanical structure to ensure that the circumference of the copper tube is in close contact with the groove at the bottom of the aluminum, thus minimizing the interface resistance between all contact surfaces. To further improve performance, a thermal epoxy resin was applied to the tube/plate joint to provide a no-gap thermal interface between the tube and the cold plate.
Liquid cooling plate adopts copper tube or stainless steel tube mechanical interlock into aluminum plate. These cost-effective liquid-cooled plates are specifically designed for low to moderate power density applications.
The Process of Solder Paste Welding to Fill Copper Pipes and Bottom Plate Grooves.
For some high density power chips, our engineers also designed the solder paste welding process to meet the good contact and thermal conductivity effect between copper tube and aluminum bottom plate. Generally speaking, a layer of nickel plating on the surface of aluminum bottom plate, and then at a high temperature of 150 degrees, melt the solder paste, so that the copper tube and aluminum bottom plate close contact, reduce thermal resistance, This process is about 15% more efficient than the epoxy-filled process, but generally, the cost is relatively higher.Sometimes, in order to increase the heat exchange area, a liquid cooled plate with double-sided copper tubes can be used.
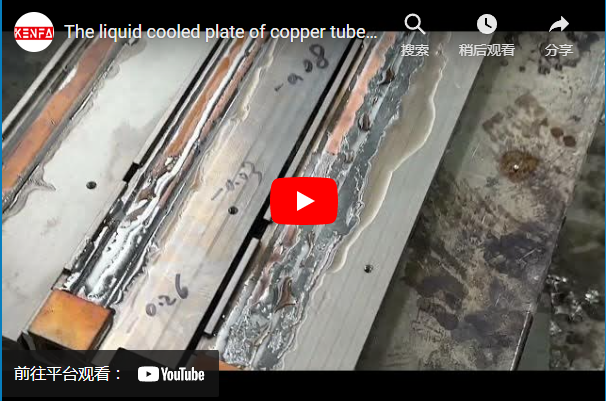
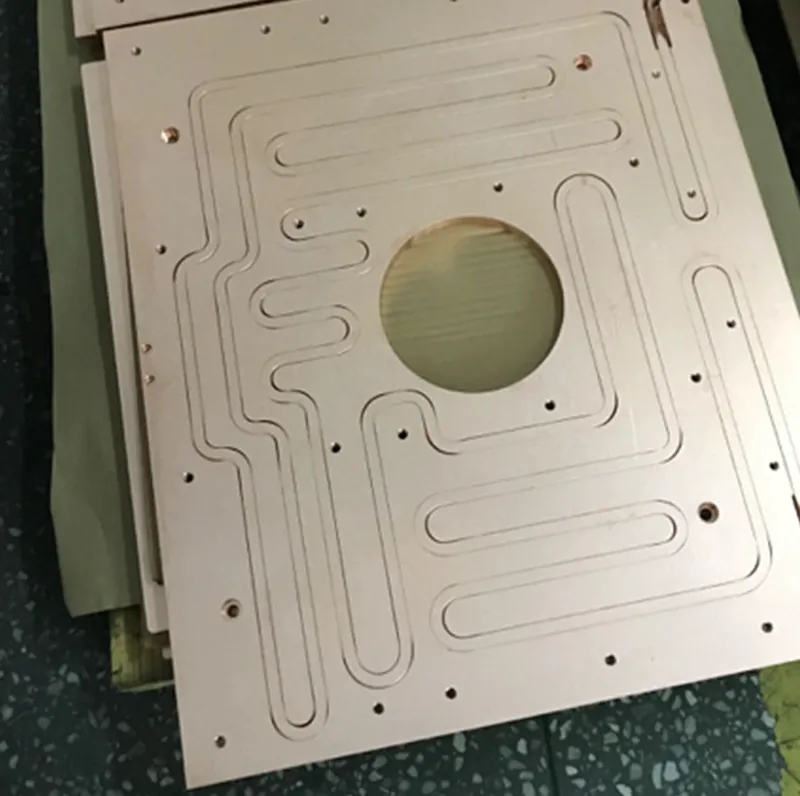


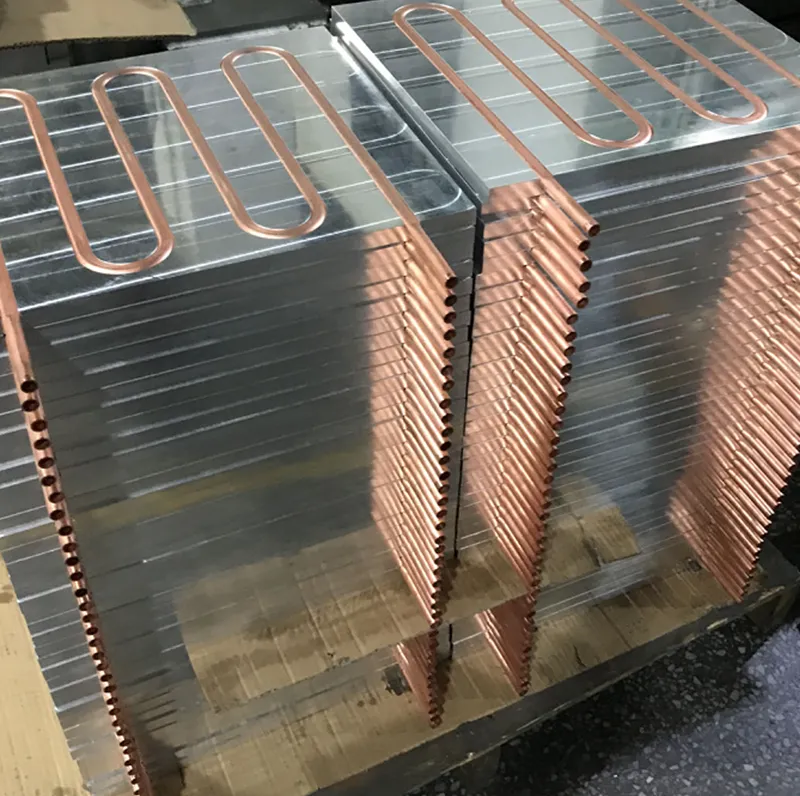
How To Make A Tube Liquid Cold Plate?
To produce a liquid cooled plate with a tube shape, it usually consists of three parts. The first one is the very important bottom plate of the liquid cooled plate, which is the core component of the entire cold plate. Therefore, most of the heat will converge on this cold plate and be transmitted to the flow channel of the circular tube.
Copper or stainless steel tubes are generally used as the second key material of the cold plate. Usually, we bend the copper tubes into different shapes of pipeline paths, passing through areas with heat sources to carry away a large amount of heat, and then avoiding installation holes, resulting in irregular paths, which are copper tube flow channels with different R-angle bends, and ultimately forming two inlet and outlet channels on one end face of the cold plate.
High thermal conductivity epoxy resin adhesive is generally used to fill the gaps between copper tube and cold plates, which facilitates the transfer of heat to the flow channels of copper pipes and reduces thermal resistance. After a period of curing, the required flatness, screw installation holes, and other processes can be processed on the CNC machine, preferably through surface treatment and cleaning
What are The Characteristics of The Copper Tube Liquid Cold Plates?
● The material of Al6063 or 6061 for plate base , tube channel is copper or Stainless steel .
● The cold plate surface can be made with chromate coating.
● It is suitable for high power chipset cooling.
● Product processing time is relatively low, high production efficiency, but high unit price;
● Generally speaking, the length, width and height of the products are 1500X1500X30mm we can make. If the size exceeds this, we will cooperate with our strategic suppliers to complete the production due to the limitation of environmental protection and factory equipment.
● Our usual process of making this product is to get the customer’s drawing, we will do the DFM feedback, and then make the sample. After sample is finally confirmed, we will mass produce.
● Our sample cycle is 3 weeks, the production cycle of mass production is 4 weeks
How to Test The leakage of The Cold Plate?
Then put the cleaned cold plate into the testing platform. At this time, we can connect the inlet and outlet of the cold plate through a 1.5Mpa air pressure to ensure that the air pressure is fully filled in a closed circulating flow channel. This pressure holding time is usually 5-20 minutes, depending on the customer’s needs and actual application conditions. Usually, we do a 10 minute pressure holding test to determine if there is any leakage.
After completing the pressure maintaining test, we will enter another stage of testing the flow resistance, which is also very important because we will analyze it through simulation software during the design process to obtain a theoretical flow resistance parameter that needs to be matched with the water pump and circulation system used by the customer’s time. Adding excessive flow resistance will increase the load capacity of the water pump, and we will also note that, If there are impurities or aluminum cutting residues inside the flow channel during the processing, we can select this unqualified cold plate through data comparison.
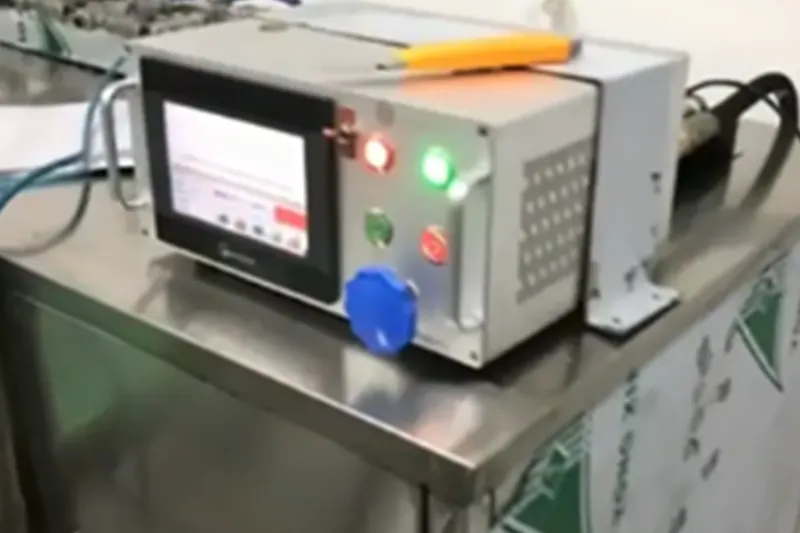

Why Choose Kenfatech's Liquid Cold Plate?
Design and Development Expertise
Our team's proficiency in creating tailored liquid cold plate solutions sets us apart. We harness our deep understanding of thermal dynamics to design products that meet your specific needs.
Quality Assurance
We implement stringent quality control measures, ensuring the reliability and durability of our products. Our liquid cold plates stand the test of time, providing a robust solution for your cooling needs.
Wide Product Range
From FSW to brazing, extrusion, and copper tube liquid cold plates, we offer a diverse product range, catering to various industry applications and power densities.
Timely Delivery
We understand the importance of time in business. Our efficient production management protocols ensure we deliver high-quality products right when you need them.
Customer Service
Our commitment extends beyond product delivery. We provide exceptional customer support, assisting you at every step of your journey with us. deliver high-quality products right when you need them.
Proven Track Record
Our track record of successful collaborations across various industries speaks volumes. Companies worldwide trust Kenfatech to provide them with top-notch thermal management solutions.
Standard specification dimensions are as follows:
You can click on the part number below to view the detailed page, and our drawings are available for download.
(Length X Width X High,Unit mm)
Part Number | Size(mm) | Material | Drawing |
KF-LCP-T5757-01 | 57X57.5X15.2t | Aluminum | Detail information |
KF-LCP-T127512-02 | 127x152x15t | Aluminum | Detail information |
KF-LCP-T177152-03 | 177x152x14t | Aluminum | Detail information |
57.15×57.15×15.2 / 127x152x15.2 / 177.8x152x14/ 590x224x7/202x130x20