Brazing Liquid Cold Plate Manufacturing
Brazing is the use of metal with a lower melting point than the base metal as a filler metal, after heating, the filler metal melts, the solder does not melt, the use of liquid filler metal wets the base metal, fills the joint gap and diffuses with the base metal, the solder is firmly .connected together.



What Is A Brazing Liquid Cold Plate?
Our Brazing Liquid Cold Plates deliver exceptional structural integrity and fluid tightness. Using a high-precision brazing process, we ensure optimal thermal performance, delivering a robust solution for high heat-flux applications. These plates stand up to demanding conditions, making them a trusted choice in industries like automotive and telecommunications.
The liquid cooling plate of this process is usually used in computer servers, cloud computing and other chips that require high-density heat dissipation. Its biggest advantage is that it can use micro channels to exchange a large amount of heat.
Brazing adopts alloy with melting point lower than the base metal as brazing filler metal, when heating, the filler metal melts, and by wetting and capillary action filled and kept in the joint gap, and the base metal is in solid state, relying on the mutual diffusion between liquid filler metal and solid base metal to form brazing joints. This kind of liquid cooled plate is generally used for server CPU cold plates, all aluminum liquid cooled plate production, all copper liquid cooled plate, etc.
What Is A Brazing Liquid Cold Plate?
Brazing is a metal-to-metal joint obtained at high temperature in controlled atmosphere, with Aluminum alloy filler. Joins different metals like aluminum, copper, stainless steel, titanium. A bonded joint has an average resin thickness of 0.1 mm with a thermal resistance of 100 °C mm²/W. A brazed joint (right) has an average aluminium thickness of 0.03 mm with a thermal resistance of 0.1 °C mm²/W.
The pull-out test of a 1.0 mm thick brazed fin, 10 mm long, reached the machine limit of 1000 N without pulling out the fin.We get a mechanical resistance above 100 N/mm2, that is close to the limit of aluminum mechanical strength. The joint is resilient and guarantees its strength from –40 °C to + 300 °C. The joint is not affected from thermal cycles or shocks. Due to the limited fin weight the brazed joints can resist to shock and vibrations more than 1000 g.


Welding Principle of Brazing Process
Welding principle of brazing process. Mixture of potassium fluoroaluminates
– KAlF4 (70–80%) / K2AlF5·H2O & K2AlF5 (20–30%) Melting point range 565°C–572°C
– Below m.p. of filler metal (577°C) -Particle size distribution for wet application x50: 2
– 6µm -Good slurry characteristicsfor dry application x50: 3.5–25µm.
Good fluidization and adhesion properties. Non hygroscopic
– Flux does not attract and absorb moisture
– Indefinite shelf life
Non-corrosive to aluminum
– Solubility of 0.15–0.45%
– No chemical reaction with water
– Indefinite pot life



What Is The Flowchart of The Brazing Liquid Cold Plate?
When producing a brazing product, the first step is to perform a degreasing and degreasing treatment on the surface of the product, as preparation of material components simultaneously.Add soldering flux and lead paste containing 15-30% silver to apply to the bottom of the aluminum or copper plate, which is the welding position of the liquid cooled plate or heat sinks to be produced.
After preparation, bake in the oven for 30 minutes to remove moisture and maintain dry characteristics. Then place in a vacuum oven under the protection of nitrogen gas, without oxygen inside the vacuum chamber, which can easily oxidize the surface of the product and cause solder joints to occur.
The final process is cooling, followed by CNC machining of the required dimensions. If it is a liquid cooled plate, X-ray scanning is also required to check if there is any false soldering in the internal flow channel. Of course, pressure testing can also be used to determine if there is any leakage.
Brazing Liquid Cooling Plate Used For Cooling Battery Packs.
The brazing process can be used to produce liquid cold plate for Battery cooling. With the development of new energy, more and more battery packs need to solve the problem of a large amount of heat dissipation. At this time, the brazing process can be used to make large-sized liquid cooled plates, usually by stamping a large area of sheet metal with a concave and convex water channel in the middle. However, this product is generally made of 3003 material, which is assembled and placed in a vacuum brazing furnace, This way, two components can be welded together, which is very reliable. Currently, this process is widely used.
Electric Vehicle Batteries and Energy Storage need stable and reliable operation in the process of photovoltaic power generation, so a reliable cooling system is necessary.So, the liquid cooled plate of the brazing process is the first step in this cooling system.

Brazing Liquid Cooling Plate Used For Data Computing Centers
Computer operation center liquid cooling plate.The brazing process can be used to cooling CUP and GPU.This kind of centralized computing data center, energy consumption is very large, the whole cooling system requirements are very high, generally need system-level liquid cold plate cooling scheme to solve.
The CUP in the data computing center runs very fast and has a very high power density. Traditional air-cooled heat dissipation systems cannot meet its cooling requirements. We use the skived fin process to produce liquid cooled plate microchannels with a very high heat exchange density. Generally speaking, a 0.2mm fin thickness and distance can efficiently convert a large amount of heat in the CUP. Therefore, this type of liquid cooled plate consists of two parts: the bottom plate and the cover plate of the skived fin microchannel.

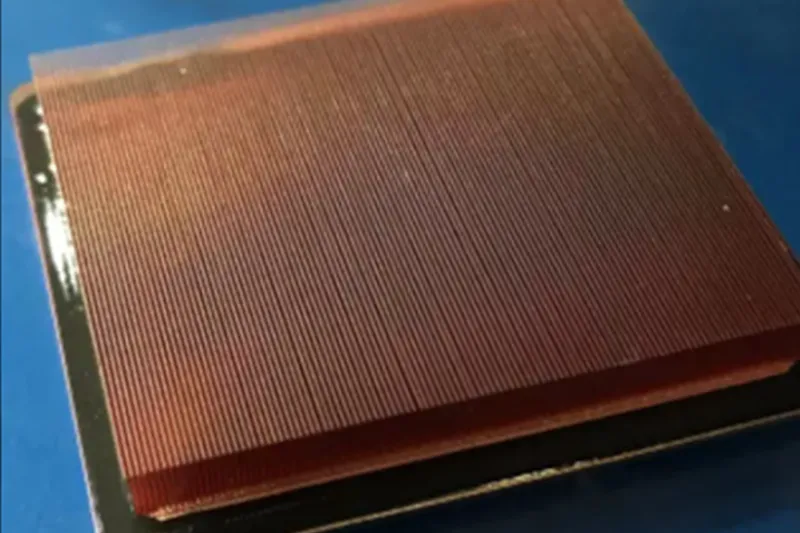

Quality Control of Our Brazing Liquid Cooling Plate?
We prioritize quality above all. Our comprehensive quality control measures ensure the reliability and durability of our products. Each liquid cold plate undergoes rigorous testing for thermal performance, structural integrity, and fluid tightness to meet our high standards. Our team of experts scrutinizes every stage of the design, development, and production process, ensuring each product that leaves our facility stands as a testament to our commitment to excellence.
We recognize that product quality issues and delivery delays are prevalent pain points in our industry. Therefore, we’ve implemented strict production management protocols and a robust supply chain strategy to mitigate these issues. By synchronizing our production schedules with our clients’ timelines, we ensure timely delivery of products without compromising on quality. Choose Kenfatech, where we merge impeccable quality with punctual delivery, providing you with seamless service and peace of mind.
