Navigating the world of thermal management solutions can be a daunting task. You might find yourself questioning which liquid cold plate technology best suits your needs. Is it Friction Stir Welding (FSW)? Or perhaps Brazing? Or could it be Extrusion or Copper Tube? How can you even compare them and make an informed decision?
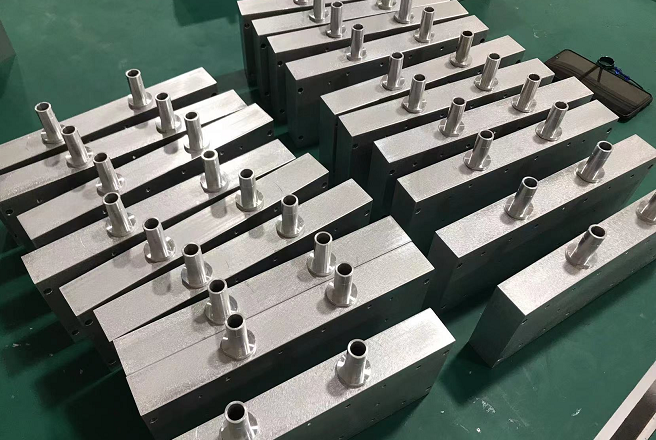
Let's begin by understanding that these terms refer to various manufacturing methods utilized in the creation of liquid cold plates. Liquid cold plates play a crucial role in thermal management across a range of industries. FSW, Brazing, Extrusion, and Copper Tube each bring unique advantages and specific limitations to the table.
By acquiring insights into these different technologies, you can ensure that you're investing in the most suitable solution for your specific thermal management requirements.
The Strength of FSW Liquid Cold Plates
Introduced in the early 1990s, Friction Stir Welding (FSW) represents a solid-state joining process that uses a non-consumable tool to join two workpieces. The tool rotates and moves along the joint line, creating frictional heat that softens the material and allows the tool to stir the workpieces together without ever reaching the melting point. This ingenious process prevents common defects associated with fusion welding, making it a highly valued technique in the liquid cold plate industry.
FSW liquid cold plates are renowned for their excellent thermal performance and structural integrity, resulting from the solid-state joint between the base plate and the cooling channel's cover. They are especially suited for applications demanding high heat flux cooling and a high degree of robustness.
The Efficiency of Brazing Liquid Cold Plates
Brazing is a metal-joining process in which a filler metal is heated above its melting point and drawn into a capillary formed by a close-fitting joint. The melted filler metal then cools and solidifies, creating a strong, sealed joint.
One of the key benefits of brazed liquid cold plates is their superior heat transfer efficiency. This high efficiency stems from the complete metal-to-metal bond formed during the brazing process, which ensures maximal heat transfer from the device to the cooling fluid. If you need highly efficient cooling solutions, brazed liquid cold plates should be a top contender in your selection process.
The Versatility of Extrusion Liquid Cold Plates
Extrusion is a technique where a material is pushed or drawn through a die of the required cross-section. This manufacturing process allows for a high degree of customization, producing complex cross-sectional profiles that are hard to achieve using other techniques.
Extruded liquid cold plates are a paragon of flexibility. They can be tailored to applications requiring custom groove patterns or pin fin designs. On top of their design flexibility, they also offer commendable cost-effectiveness and good heat transfer performance, making them an excellent choice for a broad array of applications.
The Performance of Copper Tube Liquid Cold Plates
As the name suggests, Copper Tube liquid cold plates utilize copper tubing pressed into a channeled base plate to form the fluid's cooling path. Copper is a material of choice due to its high thermal conductivity, which translates to exceptional heat transfer.
Copper tube liquid cold plates strike a balance between high performance and cost-effectiveness. They work exceptionally well in applications requiring efficient cooling in a compact form factor, making the most out of copper's excellent heat transfer properties.
The Bottom Line: How to Choose?
The decision between FSW, Brazing, Extrusion, and Copper Tube liquid cold plates ultimately hinges on your specific needs. Aspects such as thermal performance, structural strength, cost-effectiveness, and design flexibility should factor into your selection process. For instance, if your application demands high heat flux cooling and robustness, FSW liquid cold plates might be your go-to choice. On the other hand, if you prioritize superior heat transfer efficiency, brazed liquid cold plates could serve you best.
Extruded liquid cold plates bring unparalleled flexibility and cost-effectiveness to the table, making them suitable for a wide variety of applications. However, if efficient cooling in a compact form factor is your primary requirement, copper tube liquid cold plates might fit the bill.
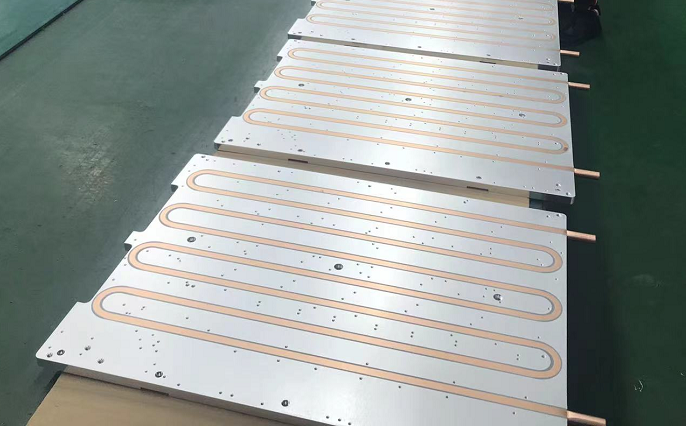
Real-world Applications
Understanding how these different types of liquid cold plates work in real-world applications can offer additional insights to guide your decision-making process.
FSW liquid cold plates, for instance, have been successfully used in various high-performance computing and electrical applications. These range from electric vehicles, where battery thermal management is critical, to power electronics, where they help keep the temperature of power modules within safe operating limits.
Brazed liquid cold plates, on the other hand, are often found in the medical industry, where cooling high-powered lasers and medical imaging equipment is crucial. They're also frequently used in high-performance computing and power electronics.
Extruded liquid cold plates are quite versatile, given their customizable nature. You'll find them cooling motor drives, IGBTs, and CPUs. Industries such as renewable energy, automotive, and data centers commonly use these plates due to their efficient heat dissipation and the possibility of creating custom channel or pin fin designs.
Copper tube liquid cold plates, due to their high performance and compact form factor, are commonly employed in applications that require efficient cooling in confined spaces. Examples include aerospace applications, laser systems, and power electronics.
Conclusion
In the end, choosing the right liquid cold plate – whether FSW, Brazing, Extrusion, or Copper Tube – depends on the specific demands of your application and system requirements. Each method offers unique advantages that could make it the ideal choice for your needs. Making an informed decision requires a thorough understanding of these differences and how they align with your requirements.
Remember, the right thermal management solution is not just about cooling; it's about enhancing the performance, reliability, and lifespan of your equipment. Always choose wisely!