Customizable Heat Sinks
When a chipset is operating, it generates a large amount of heat that needs to be dissipated to the surrounding air. At this point, something that can increase the heat dissipation area is required, and that's when a heat sink is needed.
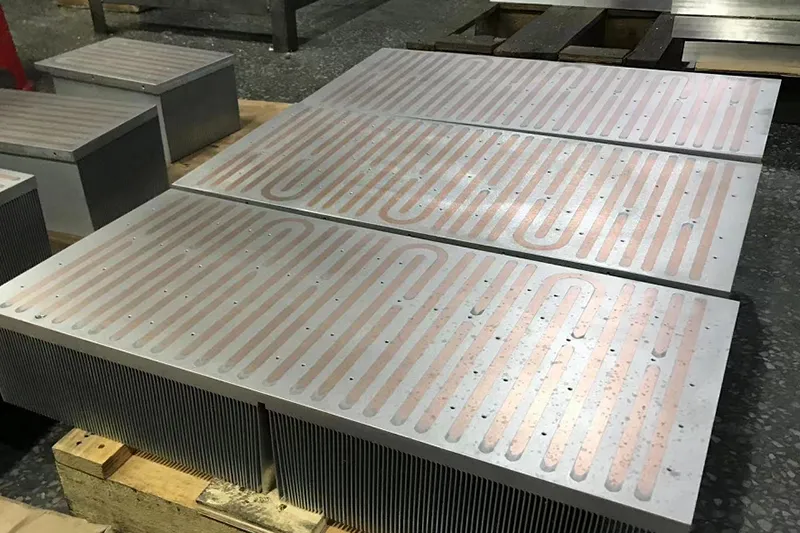

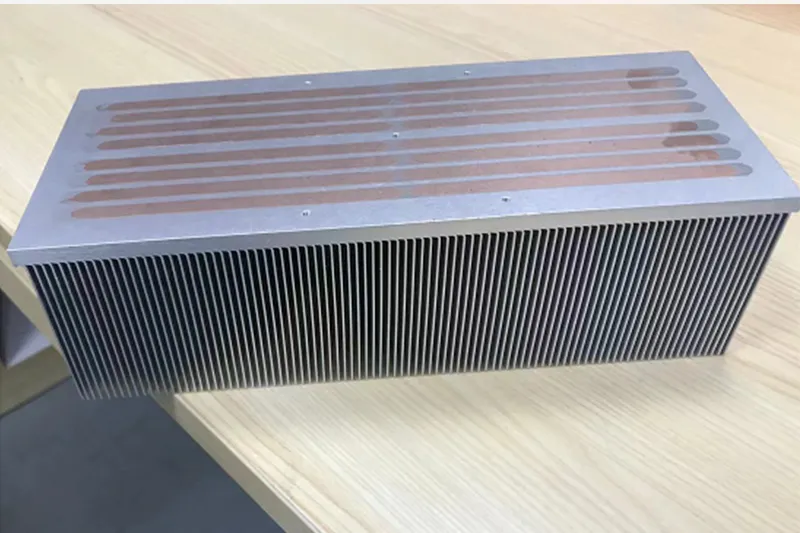
What Is A Heat Sink?
A system’s cooling solution typically takes into account appropriate process selection and optimal cost pricing considerations. As a cooling system manufacturing expert,Kenfa can provide customers with a system-level cooling solution.
A heat sink is a component used in electronic devices to dissipate or remove excess heat generated by electronic components, It is designed to absorb and transfer heat away from the hot component to the surrounding environment, allowing the device to maintain optimal operating temperatures and prevent overheating.
Heat sinks are typically made of metal, such as aluminum or copper, due to their high thermal conductivity. They consist of a large surface area with fins or ridges that increase the contact area between the heat sink and the surrounding air. The increased surface area facilitates the transfer of heat from the hot component to the air through a process called convection. The more informations about some FAQs when designing heat sinks
How to Select The Right Heat Sink For Your Electronic Device?
Overall, heat sinks play a crucial role in maintaining the temperature of electronic devices within safe operating limits, preventing damage to components caused by excessive heat. They are widely used in IGBT, Laser Equipment, Medical Equipment, Photovoltaic Inverter, 5G Implementation, Battery packing cooling, and various other electronic systems that require effective heat management.
Determine heat generation
Start by determining the amount of heat generated by your electronic device. This depends on the components used and their power consumption. You can refer to the relevant technical specifications or consult the manufacturer for this information.
Identify cooling requirements
Understanding the cooling requirements of your electronic device is crucial. Certain high-performance components may require larger heat sinks and better cooling performance to maintain temperatures within an acceptable range. Consider the device's operating environment and expected workload.
Material and design
The material and design of the heat sink have a significant impact on its cooling performance. Aluminum and copper are common material choices, with copper offering better thermal conductivity. Designs with fins or ridges increase the heat sink's surface area, enhancing heat dissipation.
Fans and cooling solutions
Some heat sinks come with fans to improve airflow and enhance cooling. Select an appropriate fan size and speed and consider how the heat sink will work in conjunction with other cooling components, such as case fans. There are also some high-density chips that require liquid cooling plate solutions, so it is a complex science to choose different heat sink solutions for different components.
What Are The Processes Used to Produce Heat Sinks?
Different power products and application environments require different processes to produce heat sinks, which also depend on the unit price and cost of the product. Of course, production efficiency is also an important factor. Our professional team can provide customers with the most reasonable suggestions and cost-effective solutions.
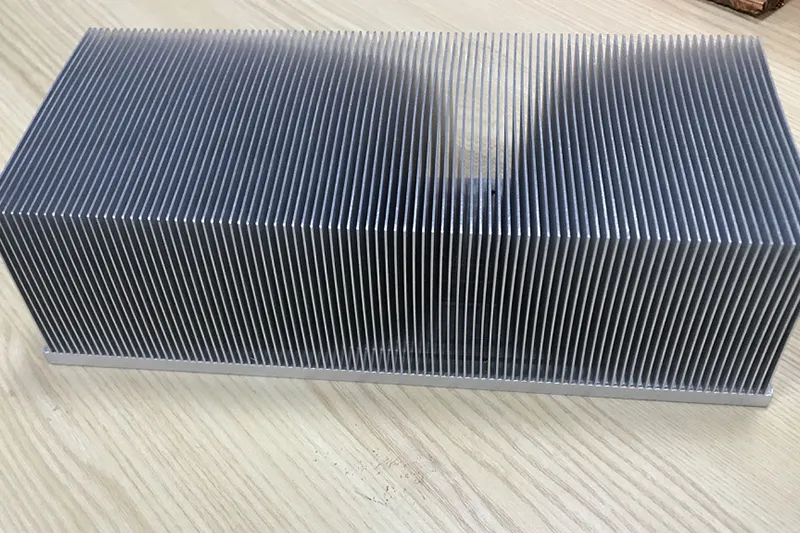
What Is A Extruded Heat Sink?
Extruded heat sink -it is a device used for heat dissipation, commonly employed in electronic devices and components. It is made of aluminum alloy 6061 /6063 or other heat-conductive materials and features a profiled shape.
Profile heat sinks typically have a rectangular or square-shaped profile, with various cross-sectional shapes such as rectangular, circular, or elliptical. They possess a large surface area for heat dissipation, effectively transferring generated heat to the surrounding environment to maintain the normal operating temperature of electronic devices.
What Is A Die Casting Heat Sink?
A die casting heat sink is a type of heat sink that is manufactured using the die casting process. Heat sinks are used to dissipate heat generated by electronic components, such as processors or power modules, and prevent them from overheating.
Die casting is a manufacturing process that involves injecting molten metal, typically aluminum or zinc, into a mold cavity under high pressure. This allows for the production of complex shapes with high precision and dimensional accuracy. Die casting heat sinks are made using this process to create intricate designs and optimize their cooling performance.
The die-casting process starts with the creation of a mold, usually made of steel, which is designed to produce the desired shape of the heat sink. The molten metal is then injected into the mold at high pressure, filling the cavities and solidifying rapidly to form the heat sink. After solidification, the mold is opened, and the heat sink is removed.
Die-cast heat sinks offer several advantages. They have excellent thermal conductivity, allowing for efficient heat transfer from the electronic component to the surrounding air. The intricate designs and fin structures made possible by the die casting process maximize the surface area of the heat sink, enhancing its cooling capacity. Die-cast heat sinks also have good mechanical strength and can withstand harsh operating conditions.
What Is A Soldering Heat Sink With Heat Pipes?
A heat pipe heat sink is a type of heat sink that utilizes heat pipes to enhance its cooling efficiency. Heat pipes are passive heat transfer devices that effectively transfer heat from one location to another using phase change principles.
A heat pipe consists of a sealed copper or aluminum tube containing a small amount of working fluid, typically a low-boiling-point liquid such as water or a refrigerant. The heat pipe has an evaporator section, a condenser section, and a wick structure. The evaporator absorbs heat from the heat source and vaporizes the working fluid. The vapor then moves to the condenser section, where it releases the heat and condenses back into a liquid. The condensed liquid flows back to the evaporator through the wick structure, driven by capillary action, completing the heat transfer cycle.
In a heat pipe heat sink, heat pipes are integrated into the design of the heat sink to improve its cooling performance. The heat pipes act as highly efficient heat conduits, effectively transferring heat from the heat source to the heat sink’s fins. The heat pipes distribute the heat evenly across the heat sink, allowing for efficient heat dissipation and reducing temperature gradients.
What Is A Cold Forged Heat Sink?
A cold forged heat sink is a type of heat sink that is manufactured using a cold forging process. A heat sink is a component used to dissipate heat generated by electronic devices such as microprocessors, power transistors, and LEDs. Cold forging, on the other hand, is a metalworking process in which a metal is shaped and formed at room temperature or slightly elevated temperatures, without the use of heat.
In the case of cold forged heat sinks, the manufacturing process involves pressing or stamping a solid block or slug of aluminum or copper alloy under high pressure to shape it into the desired heat sink design. This process utilizes a die and punch set to apply pressure and deform the metal without the need for additional heat.
The advantage of cold forging in heat sink manufacturing is that it allows for precise control over the shape, size, and fin geometry of the heat sink. The process produces heat sinks with excellent thermal conductivity and high mechanical strength. The resulting heat sinks typically have a dense structure with fine fins and optimized surface area, which enhances the heat dissipation capability.Cold forged heat sinks are widely used in electronic devices that require efficient cooling, such as computers, servers, power supplies, and automotive electronics. They offer better thermal performance compared to heat sinks manufactured using other methods, such as extrusion or machining.
What Is A Skived Fin Heat Sink?
The process of skived fin heat sink is based on a flat aluminum material. After heat treatment, its hardness is reduced. Under the mechanical action, the tilting Angle of the tool is controlled by the customized tool and the program written, and the aluminum plate is evenly cut into a flake structure under the pressure of the hydraulic press.
The advantage of this kind of heat sink is that it can meet the customer’s demand for high-power chip heat dissipation. Theoretically, the heat sink of the profile process is limited by the process. In general, the fin height of the heat sink can only be about 25 times the spacing, which means the height of the heat sink is 25mm, so the spacing is 1mm. It cannot meet the requirements of high-density heat sinks.
Therefore, heat sinks with fin processing can be arbitrarily set with fin of less than 130 height and width of less than 700mm according to customers’ requirements.The skived fin process heat sinks, which is used for heat dissipation schemes of high-power frequency converter, controller, wind inverter, IGBT and other semiconductors
Our Expertise In Heat Sink Design And Production
Kenfa Tech has extensive manufacturing experience and specialized knowledge in heat sink design and production. This enables you to deliver high-quality heat sink products that meet customer requirements and standards. And we have the ability to customize heat sinks according to specific customer needs and requirements. This flexibility allows you to cater to a wide range of industries and applications.About the process and technological innovation, we can continuously pursue process and technological innovation to enhance the performance and efficiency of heat sinks.
How to Help Customers Design a Heat Sink?
Thermal simulation analysis is a very important process, especially for new design projects. Early stage simulation analysis can shorten the product development cycle and save costs. We usually tell our customers whether they need to provide them with a thermal analysis solution. If customers do not have the design ability, we usually design the optimal solution for them for free, which can save them development time and costs, Generally speaking, it can save 30% of product development time and 50% of research and development costs.

How to Control The Heat Sink Quality?
At Kenfatech, we prioritize quality above all. Our comprehensive quality control measures ensure the reliability and durability of our products. Each liquid cold plate undergoes rigorous testing for thermal performance, structural integrity, and fluid tightness to meet our high standards. Our team of experts scrutinizes every stage of the design, development, and production process, ensuring each product that leaves our facility stands as a testament to our commitment to excellence.
We recognize that product quality issues and delivery delays are prevalent pain points in our industry. Therefore, we’ve implemented strict production management protocols and a robust supply chain strategy to mitigate these issues. By synchronizing our production schedules with our clients’ timelines, we ensure timely delivery of products without compromising on quality. Choose Kenfatech, where we merge impeccable quality with punctual delivery, providing you with seamless service and peace of mind.
Why Choose Kenatech's Heat Sink Solutions?
Design and Development Expertise
Our team's proficiency in creating tailored heat sink solutions sets us apart. We harness our deep understanding of thermal dynamics to design products that meet your specific needs.
Quality Assurance
We implement stringent quality control measures, ensuring the reliability and durability of our products. Our liquid cold plates stand the test of time, providing a robust solution for your cooling needs.
Wide Product Range
From extrusion heat sink to die casting ,soldering ,skived fin ,forged heat sink, we offer a diverse product range, catering to various industry applications and power densities.
Our track record of successful collaborations across various industries speaks volumes. Companies worldwide trust Kenfatech to provide them with top-notch thermal management solutions.
Timely Delivery
We understand the importance of time in business. Our efficient production management protocols ensure we deliver high-quality products right when you need them