Liquid cold plate, also known as cold plate/cooling plates, is a very efficient way to dissipate heat for high-power chips. Its principle is that under the action of the pump, the liquid in the tube is circulated, so that the liquid absorbs the heat of the equipment or the chip, and brings the heat to the heat exchanger. Under the action of the powerful air cooling system or compressor, the temperature of the liquid brought out of the tube or channels are reduced to the ambient temperature or below the ambient temperature range.
Kenfa Technology has more than 10 years of manufacturing and design experience, can provide customers with complete liquid cooling plate design solutions and products, can reduce the surface temperature of customers’ high-power heating equipment and chips to the required range, truly achieve uniform temperature, the reliability of equipment operation, such as high-power UV-LED can reduce its light attenuation, play its maximum light efficiency.
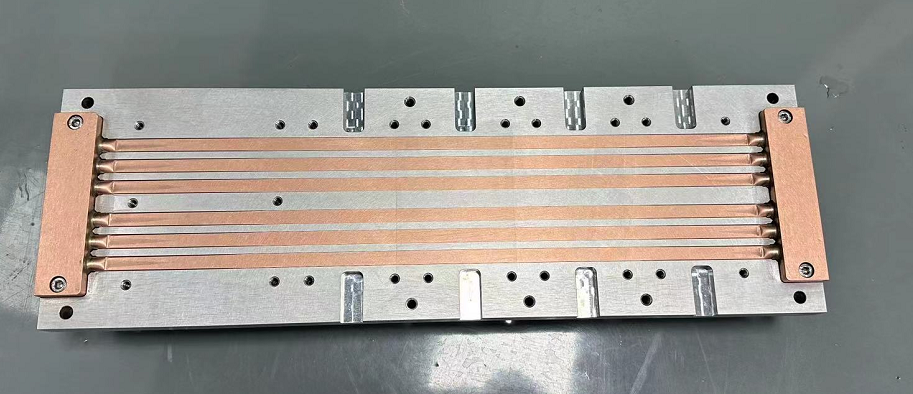
How to choose or design the appropriate liquid cold plate?
Assuming that you have such a demand, engineers generally will ask you the size of the equipment, water cooled space size, also to be allowed to say in a chassis, left chip heat dissipation space is 200 x200x15mm, then based on the size of the tube or channel design needs to consider the liquid velocity, the material of plate, the length of the flow channel size, These need to use professional thermal analysis software to calculate and analyze. Ok, in this case we determined the size, based on the chip power to design the internal details of the liquid cooled plate.
However, sometimes when an engineer is working on a project, he does not know what size is needed. How can he do this? Similarly, the method is very simple, when we design this type of liquid cooling plate, the flexibility of the scheme is very much, for example, with our company’s standard products, our company’s standard products involve a complete scheme of small power to high power. However, some customers’ liquid cooled plates need to be processed in some places to meet the installation requirements of other devices, so it is still necessary to customize the design.
Our engineers based on the chip power size, previous design experience, customer demand quantity, of course, the flow rate of liquid cooling plate, inlet and outlet temperature specifications, environmental temperature Settings, will roughly give a solution to customers, generally choose aluminum6061 or 6063 as the main body of the liquid cooling plate.

How to choose channel material of the liquid cold plate?
When we determine the size of the liquid cooling plate, a very important link is to know the environment of our equipment, such as outdoor or indoor. If it is used in the outdoors, we should consider the type of liquid, this is because different liquids are corrosive to the internal flow of the cold plate, usually laboratory level liquids need to sterilize, remove oxidation ions and so on.
For example, some customers choose ordinary tap water, and even some direct users outside the sea water, which has a lot of salt, which will corrosion our liquid cooling plate channels, thus destroying our entire circulation system of pumps, heat exchangers, etc. Therefore, we generally recommend that customers use copper pipe or stainless steel pipe as the material of the runner.
Of course, if we choose stainless steel, we need to consider its conductivity, because its conductivity is lower than that of copper. Under the same conditions, we have to increase the flow rate of the pump, the fan volume and the wind pressure of the heat exchanger, so that the temperature of the whole channel can be reduced to a lower condition to meet the temperature requirements of our chip joint
How to choose the production process of liquid cold plate?
when we determine the channel of material, we are basically determine the process of the surface plate, if we use a laboratory level of the liquid, we can use aluminum, with a CNC processing flow, and then use the friction stir welding process means the two parts welded together, (Detailed process can refer to our other pages on the friction stir welding process description), if the liquid used by the customer is corrosive, then we must use copper tube to do the flow channel, at this time we must use our very mature process, aluminum plate + copper tube tight fit, there is no gap between them, Of course, we will also use epoxy resin to fill some weak gaps. If it is seawater as a liquid circulation medium, then we must use stainless steel 304 material. Therefore, we should be very clear about the use of the environment and conditions when designing the liquid cooling plate. What kind of material of the runner is used, which is also the key guarantee for the operation of the equipment in the later stage, such as the frequency of maintenance.
To sum up, when designing liquid cold plate, engineers must consider the following aspects: size, material, process and environmental conditions. These are very important factors. Kenfa Tech can provide customers with systematic liquid cold plate design and production services. Email, linkedin, Youtube, you can both find our sales.
