Cold forged process heat sinks
Simple structure, low cost, is usually a large quantity and long production cycle of the choice of products.
The utility model relates to a cold forging process production process of liquid cold plate, using high heat conduction AL1100, product size is 200X150X30mm
There are a lot of heat sink in cold forging process, but there are few liquid cold plates in cold forging process. This is because the tooling cost of cold plates in cold forging process is very expensive, but the high-density fins can take away a lot of heat, which makes the heat exchange in the cavity of cold plate very good.Normally, we can use cylindrical fins, but we found that oval fin is more efficient.

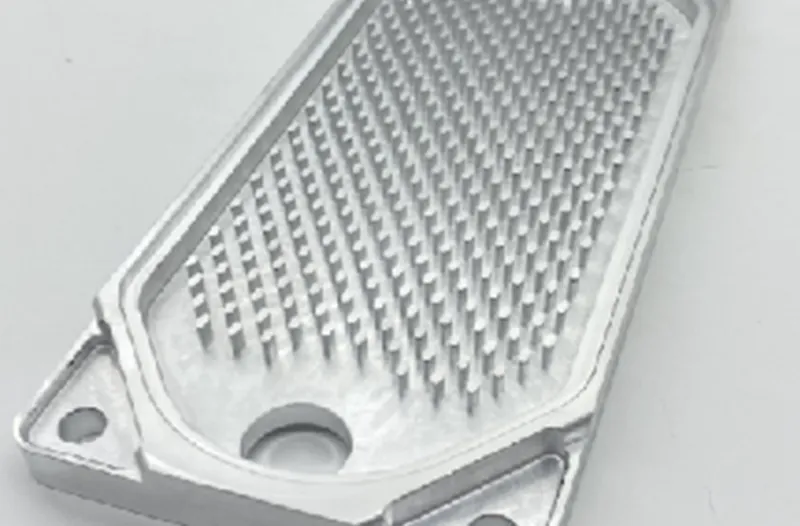
After made production, we will do antioxidant treatment and cleaning.We will use the friction stir welding process to complete the welding of the bottom plate and the top cover,Of course, after we finish the welding, we will use precision CNC machining. The flatness of the surface will be controlled at 0.05, and the tolerance of the mounting screw hole distance will be 0.1. All these are for the stability and reliability of the subsequent customers’ products.


The cost of aluminum is relatively low, but some customers’ demand is very strict, small size, high power IGBT, so our engineers usually recommend the use of copper material for making liquid cooling plate, obviously, copper water cooling plate efficiency is higher, but its cost is relatively high.
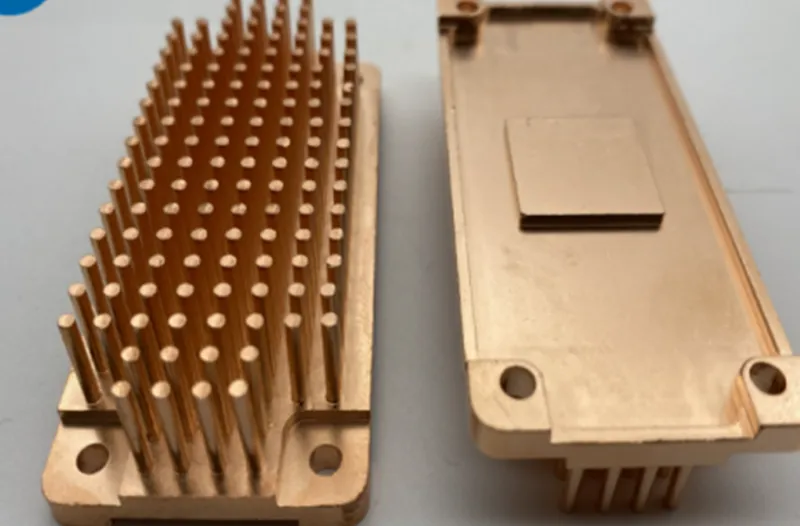

Why choose us to help you do cold forging process of liquid cooled plate?
1,We can customize the production for you and can be different sizes and different power, at the same time we have a strong design ability.
2,We have more than 10 years of manufacturing experience;
3,With 300T to 3500T forging equipment, at the same time, there are several sets of auxiliary equipment;
4,Senior tooling design engineer and many of skilled operators;
5,Have a complete quality control system and control process;
6,Sample production cycle is 3 weeks, mass production is 4-5 weeks