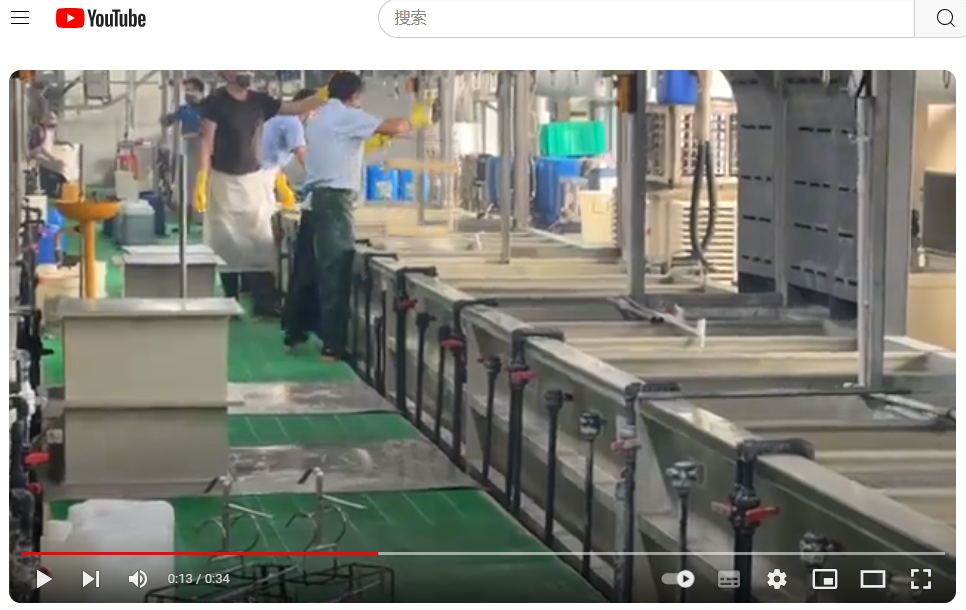
There are many production processes for heat sink. Due to the size of the power and the placement of the components, the produced heat sinks have different processes. In the production process of some heat sinks with high power density, such as when a single power component is greater than 1000W, customers do not choose the liquid cooling plate cooling method.
At this time, the production of air-cooled forced convection heat sinks is relatively difficult. This is because the bottom plate of the heat sinks must be made of high thermal conductivity copper material for temperature equalization and heat conduction. Considering the cost, the fins of the heat sink can only be made of aluminum material. Considering the high thermal conductivity coefficient material, it is generally used for aluminum 1100 or 1050. However, this encounters a problem that copper material and aluminum material have different properties. The metal cannot be directly welded together.
Difficulties in directly welding aluminum and copper.
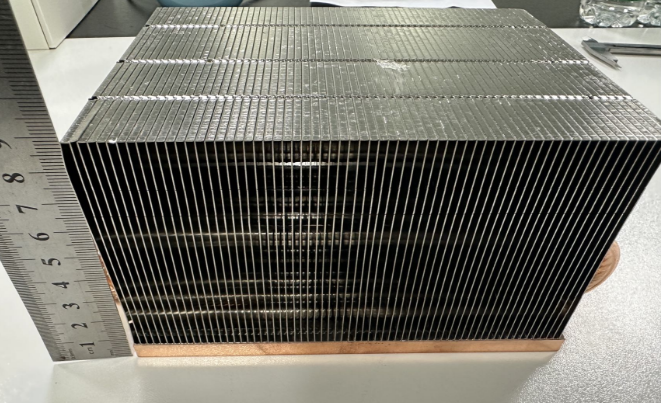
First of all, a dense alumina film is extremely easy to form on the surface of aluminum. The melting point of this alumina layer is about 2050 °C, while the melting point of aluminum is 660 °C. During the welding process, the alumina film will hinder the good fusion between aluminum and copper. Moreover, the alumina film is relatively stable and will prevent the wetting of the filler metal and the aluminum matrix, making welding difficult.
Secondly, there are great differences in the thermophysical properties of aluminum and copper. The thermal conductivity and specific heat capacity of aluminum are larger than those of copper. During welding, the different heat conduction speeds will lead to uneven temperature field distribution in the welding area and are prone to welding defects.
However, the situation is different after nickel plating on the aluminum surface. The nickel layer can effectively prevent the formation of alumina on the aluminum surface. Because nickel itself will not quickly generate an oxide film as refractory as alumina during the welding process. The nickel layer can also improve the wettability between aluminum and copper, making it easier for the filler metal to spread between the two.
Advantages of Nickel Plating
Nickel serves as a transition layer, easing issues caused by differences in aluminum and copper’s thermophysical properties. It helps distribute heat more evenly during welding.
This improves welded joint formation and enhances welding quality. Nickel’s presence makes the overall welding process more effective.
Therefore, after nickel plating on the aluminum surface, it is more conducive to welding with copper.

Similarly, when we are making heat pipe heat sink, copper heat pipe cannot be welded together with aluminum fins. At this time, the surface of the aluminum fin must also be nickel plated in order to be welded together with solder paste.
The temperature of solder paste is usually between 180-280 degrees. This allows it to weld two metal materials together for heat transfer and dissipation. The structural design and nickel plating thickness must consider heat dissipation power and heat sink characteristics to meet customer needs.
In some cases, the customer’s heat sink needs to be waterproof. To achieve this, we spray powder or oil on the heat sink surface. This prevents moisture in the air from corroding the nickel-plated aluminum fins.
Conclusion
So, when you choose a heat sink with any process, you must consider it based on actual application. When you are not very clear, you can ask your engineer to contact our Kenfa Technology company engineers. We can provide customers with professional customized design thermal solutions to help them solve thermal management problems.