Introduction
In the realm of thermal management, ensuring that equipment remains within optimal temperature ranges is crucial. This is especially true for high-performance computing systems, medical devices, and other industrial applications where overheating can lead to system failures or reduced efficiency. Cold plates and heat pipes are two prominent technologies among the various thermal management solutions available. Understanding the differences between these solutions is essential for making informed purchasing decisions.
This article aims to provide a detailed comparison of cold plates and heat pipes, covering their definitions, working principles, applications, advantages, and disadvantages. By the end, you will better understand which solution best suits your needs.
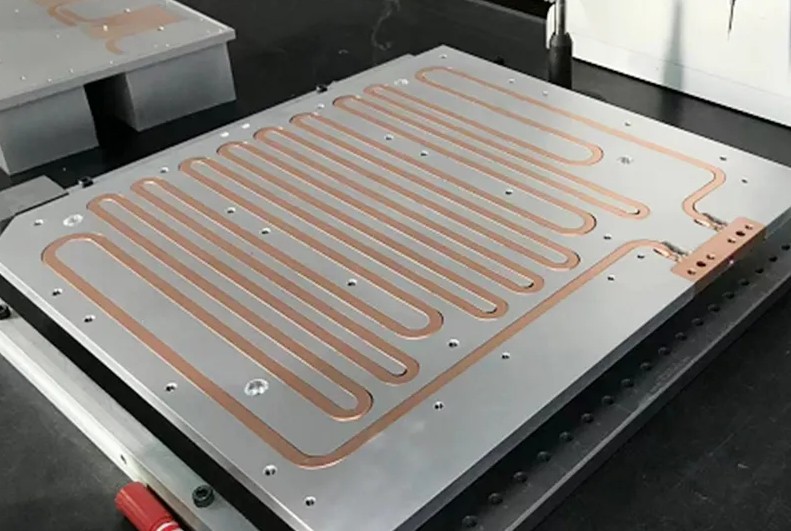
Understanding Cold Plates
Definition of Cold Plates
A cold plate is a heat exchanger that removes heat from electronic components and other heat-generating devices. It typically consists of a flat metal plate through which a cooling fluid circulates, absorbing heat from the attached components and dissipating it from the system. Cold plates can be categorized into different types based on their cooling mechanisms, such as air-cooled and liquid-cooled cold plates.
Working Principle
Cold plates provide a direct thermal interface between the heat source and the cooling fluid. The heat generated by the components is conducted through the metal plate and into the circulating fluid. In the case of a liquid cold plate, a pump circulates a coolant through the plate, enhancing the heat transfer efficiency. This setup effectively removed high heat loads from compact areas, making it ideal for demanding applications.
Common Applications
Cold plates are widely used in various industries due to their high cooling capacity and versatility. Some typical applications include:
- Data Centers:Used to cool servers and other high-performance computing equipment.
- Medical Devices:Ensures the stable operation of medical imaging and diagnostic equipment.
- Industrial Equipment:Provides cooling for power electronics and other high-heat-generating machinery.
Understanding Heat Pipes
Definition of Heat Pipes
Heat pipes are thermal management devices that transfer heat through evaporation and condensation of a working fluid. They are typically sealed, vacuum-tight tubes filled with a small amount of liquid. Heat pipes are known for their passive operation, meaning they do not require any external power.
Working Principle
A heat pipe operation relies on the working fluid’s phase change. When heat is applied to one end of the pipe (the evaporator section), the fluid inside absorbs the heat and vaporizes. The vapor then travels to the more fantastic end of the pipe (the condenser section), where it releases the heat and condenses back into a liquid. The liquid returns to the evaporator section via capillary action or gravity, completing the cycle. This efficient heat transfer mechanism allows heat pipes to transport heat over relatively long distances with minimal temperature drop.
Common Applications
Heat pipes are commonly used in applications requiring passive, reliable heat transfer. Some typical uses include:
- Laptops and Mobile Devices:Provides cooling for CPUs and GPUs without active cooling solutions.
- Spacecraft and Satellites:Transfers heat in a zero-gravity environment where conventional cooling methods are ineffective.
- Telecommunications Equipment:Ensures the stability and longevity of electronic components in network infrastructure.
Critical Differences Between Cold Plates and Heat Pipes
Design and Structure
Cold plates and heat pipes differ significantly in their design and physical structure. Cold plates typically involve a flat metal plate with internal channels for fluid circulation, requiring pumps and additional plumbing for liquid-cooled systems. In contrast, heat pipes are simple sealed tubes that leverage capillary action and phase change, making them compact and maintenance-free.
Heat Transfer Mechanisms
A cold plate’s primary heat transfer mechanism involves direct conduction to the cooling fluid, which is then circulated to dissipate the heat. Liquid cold plates, in particular, offer high thermal conductivity due to the effective cooling provided by the liquid. On the other hand, heat pipes use the latent heat of vaporization and condensation of the working fluid, allowing efficient heat transfer over long distances with minimal thermal resistance.
Efficiency and Performance
Regarding efficiency and performance, cold plates generally offer higher cooling capacity and can handle larger heat loads. This makes them suitable for high-power applications where significant heat dissipation is required. Heat pipes, while efficient in specific scenarios, have limitations in their heat transfer capacity and are better suited for applications with moderate heat loads and where passive cooling is preferred.
Scalability and Flexibility
Cold plates, especially those designed by specialized manufacturers, offer greater scalability and can be customized to fit specific requirements and configurations. This flexibility makes them ideal for a wide range of applications. Heat pipes, though versatile, have fixed designs and are less adaptable to complex cooling needs.
Advantages and Disadvantages
Advantages of Cold Plates
Cold plates, particularly liquid cold plates, offer several advantages:
- High Cooling Capacity:Cold plates are highly efficient in dissipating large amounts of heat, making them suitable for high-performance and high-power applications.
- Versatility:They can be customized to fit various shapes and sizes, making them adaptable to different cooling requirements.
- Precision Cooling:Cold plates provide localized cooling, targeting specific heat sources with high precision.
- Reliability:Designed by reputable cold plate manufacturers, these systems are robust and reliable, ensuring consistent performance over time.
Disadvantages of Cold Plates
Despite their advantages, cold plates have some drawbacks:
- Complexity:The design and integration of liquid cold plates involve pumps, tubing, and coolant management systems.
- Cost:They can be expensive to implement, especially in custom configurations.
- Maintenance:Liquid cold plates require regular maintenance to ensure the cooling system operates efficiently and to prevent leaks or coolant degradation.
Advantages of Heat Pipes
Heat pipes also have several notable advantages:
- Passive Operation:Heat pipes do not require external power or moving parts, making them highly reliable and maintenance-free.
- Compact Design:Their compact structure allows easy integration into space-constrained environments.
- Efficiency:Heat pipes provide efficient heat transfer over long distances with minimal thermal resistance, which is ideal for cooling components spread out within a system.
- Durability:They are generally durable and can operate effectively in various orientations and environmental conditions.
Disadvantages of Heat Pipes
However, heat pipes have limitations as well:
- Limited Heat Transfer Capacity:Heat pipes may not be suitable for applications requiring the dissipation of extremely high heat loads.
- Fragility:The sealed tubes can be delicate and prone to damage if improperly handled.
- Fixed Designs:Heat pipes are less flexible in customization than cold plates, limiting their adaptability to specific needs.
Choosing the Right Solution
Factors to Consider
When deciding between a cold plate and a heat pipe, several factors should be taken into account:
- Application Requirements:Assess the specific cooling needs of your application, including the amount of heat to be dissipated and the spatial constraints.
- Budget:Consider the initial cost and long-term maintenance expenses associated with each cooling solution.
- Space Constraints:Evaluate the available space for the cooling solution and whether a compact design is necessary.
- Environmental Conditions:Consider the operating environment, such as the presence of gravity (significant for heat pipes) and the potential for vibration or mechanical stress.
Application-Specific Recommendations
For high-power applications, such as data centers or industrial equipment, where substantial heat needs to be dissipated, a liquid cold plate designed by a reputable cold plate manufacturer may be the best choice. These systems offer high cooling capacity and precision, ensuring efficient thermal management.
Heat pipes may be more suitable for applications requiring passive, reliable cooling, such as laptops, mobile devices, or aerospace components. Their compact design and passive operation make them ideal for environments where maintenance is challenging or impractical.
Future Trends and Innovations
The field of thermal management is continuously evolving, with new technologies and innovations emerging. Materials science and engineering advances are leading to the development of more efficient and compact cooling solutions. For instance, hybrid systems that combine the benefits of cold plates and heat pipes are being explored to provide even more effective thermal management. Staying informed about these trends can help you make better-informed decisions when selecting a cooling solution.
Conclusion
Understanding the differences between cold plates and heat pipes is crucial for selecting the right thermal management solution. Cold plates, particularly liquid ones, offer high cooling capacity and precision, making them ideal for demanding applications. On the other hand, heat pipes provide passive, reliable cooling for applications with moderate heat loads.