Liquid cooling plates are integral to many cooling systems, serving as vital components for effective heat dissipation. When choosing a liquid cooling plate for your system, there is a significant difference between copper and aluminium materials. Each material has unique benefits and drawbacks that users should carefully examine. This book will cover the distinctions between an aluminium liquid cooling plate and a copper liquid cooling plate in detail, along with information to assist users in making wise choices.
Recognizing Copper Liquid Cooling Plates
In high-performance applications, copper is preferred for liquid cooling plates because of its exceptional thermal conductivity and resistance to corrosion. Manufacturers use copper’s characteristics to create effective cooling solutions that drain heat from electronic components. Copper Liquid Cooling Plates perform exceptionally well at removing heat from the source, which makes them perfect for harsh settings where heat control is essential.
Property | Copper Liquid Cooling Plate |
Thermal Conductivity | High |
Corrosion Resistance | Excellent |
Durability | Superior |
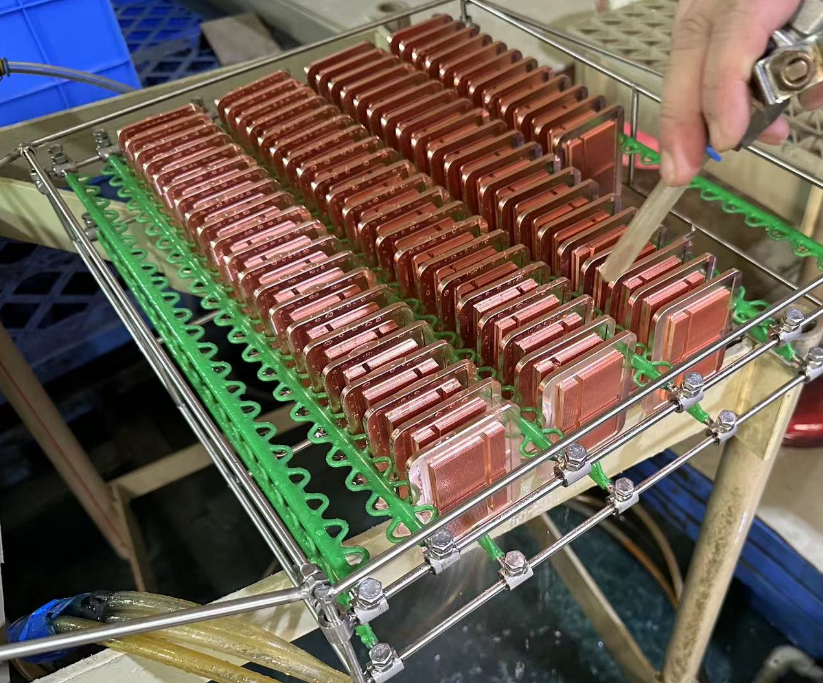
Recognising aluminium liquid cooling plates
Aluminium has a distinct set of properties from copper that make it appropriate for some cooling purposes. Aluminium has benefits such as being lightweight and affordable, even though its heat conductivity may be lower than copper’s. Manufacturers of Liquid Cooling Plates frequently utilise the characteristics of aluminium to produce cost-effective cooling solutions for various systems.
Property | Aluminum Liquid Cooling Plate |
Thermal Conductivity | Moderate |
Weight | Light |
Cost | Lower |

Considerations for Selecting Between Aluminium and Copper
Many factors are considered when choosing between copper and aluminium liquid cooling plates. If users are aware of these factors, they will be better able to make decisions that fit their needs and the limitations of their Heat Sink system.
Factors | Copper Liquid Cooling Plate | Aluminum Liquid Cooling Plate |
System Requirements | High performance systems | Low to medium-performance systems |
Budget Constraints | Higher initial cost | Lower initial cost |
Environmental Conditions | Excellent corrosion resistance | Susceptible to corrosion in certain environments |
Long-Term Investment Considerations | Superior durability | May require higher maintenance or replacement costs over time |
Real-World Applications and Case Studies
Let’s examine some case studies and real-world applications to understand better the practical effects of selecting an aluminium and copper liquid cooling plate.
1. Computer Systems with High Performance (HPC)
Copper Liquid Cooling Plates are frequently chosen in high-performance computing situations where heat generation is significant. These systems need effective heat dissipation to ensure peak performance and avoid thermal throttling. Because copper has a higher thermal conductivity than other materials, heat is quickly transported away from essential components, enabling HPC systems to run continuously at maximum efficiency.
2. Overload Configurations
Experimenters and overclockers frequently push the boundaries of their hardware to maximise performance. Copper Liquid Cooling Plates are incredibly useful in these situations to regulate temperature. Large amounts of heat are produced by overclocked CPUs and GPUs, so effective cooling is crucial to avoiding damage and preserving stability. Because copper dissipates heat quickly, it’s a great material choice for overclocking settings where every degree counts.
3. Industrial Solutions for Cooling
Copper Liquid Cooling Plates are widely used in industrial settings where durability and dependability are critical factors. Industrial machinery and equipment work in challenging conditions with high temperatures and demanding schedules. Because of its resilience to corrosion and long lifespan, copper is an excellent choice for these harsh circumstances, guaranteeing steady performance and little downtime.
Conclusion and Recommendations
In summary, system needs, financial limits, environmental factors, and long-term investment considerations all play a role in the decision between copper and aluminium liquid cooling plates. Before choosing one material over the other, consumers should carefully analyse the pros and disadvantages of each.
Copper Liquid Cooling plates are recommended for industrial applications and high-performance systems where heat dissipation and durability are crucial. Due to their exceptional thermal conductivity and resistance to corrosion, they are ideal for harsh settings where dependability is crucial.
Yet, the Aluminium Liquid Cooling Plate offers a more affordable option for consumers with tighter budgets or less demanding cooling needs. Aluminum’s lightweight design and low cost make it a desirable choice for some applications, even though its heat conductivity may be better than copper’s.
When choosing the suitable liquid cooling plate material, users should evaluate their unique needs and prioritise performance, affordability, and longevity. By carefully weighing these variables, users may guarantee their systems’ best cooling performance and dependability.
Users must remain up to date on the most recent developments and trends in liquid cooling technology as it advances. Manufacturers are essential in fostering innovation and creating fresh approaches to satisfying the ever-increasing requirements of contemporary cooling systems.
We hope that this thorough guide has offered insightful information about the distinctions between copper and aluminium liquid cooling plates to assist users in making wise decisions about their cooling requirements. Please do not hesitate to contact a reputable manufacturer or industry expert if you need help or have more questions about Liquid Cooling Plates.